Salvagnini was one of the first companies to believe and invest in cutting with compressed air, which is bringing very impressive results especially in terms of running costs. Fiber sources have revolutionized the items that make up the hourly cost of laser systems and the impact that each of these has. Their high efficiency has drastically reduced energy consumption, while their intrinsic features have reduced the costs of routine and extraordinary maintenance. The faster cutting speed has also reduced processing times, and therefore the cost per part. The cost of the assist gas was one of the few items that remained unchanged.
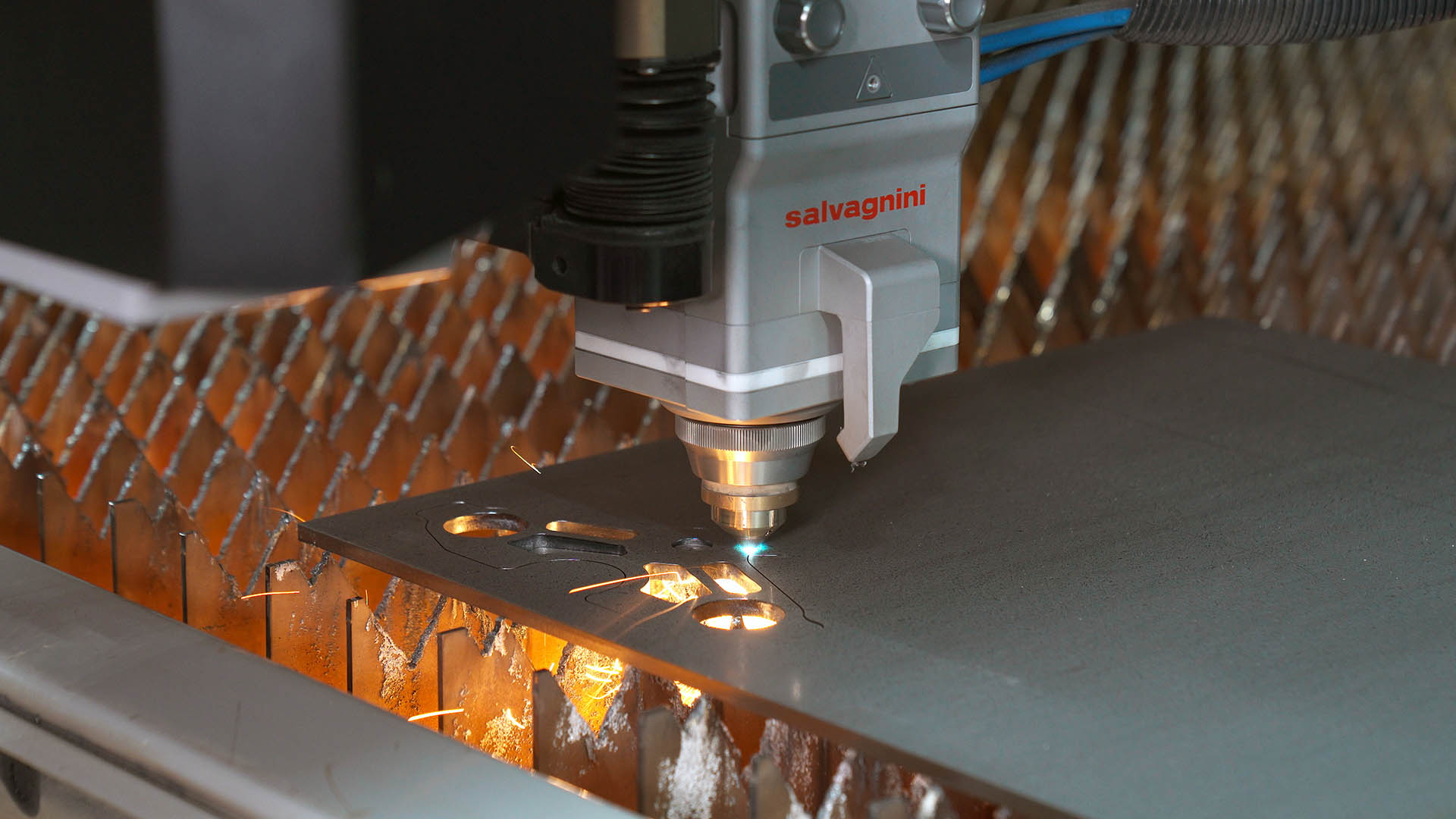
Cutting with compressed air is cheaper than with nitrogen, and this is all the truer when the cost per m3 of nitrogen increases: the higher the cost of nitrogen, the more cost-effective cutting with compressed air is. It is therefore natural that the use of compressed air as an assist gas is one of the most interesting hot topics in laser cutting.
The evolution of ACUT, the Salvagnini option that extends the possibilities of the L3 and L5 and allows cutting with appropriately treated compressed air, has been rapid: depending on the source power, it can now cut thicknesses of up to 20 mm. Without forgetting APM, the compact, turnkey device that is complementary to ACUT and connects directly to the pneumatic supply, to work in the best possible conditions.
Would you like to learn more about cutting with compressed air? We have a short white paper for you.

Do you have any questions?