Your flexible bending solution
The P2 natively combines productivity, with its automatic bending and handling cycles, and flexibility, with its universal bending tools.
Compact Panel Bender Overview
Ready to upgrade your metal bending experience? Salvagnini's P2 panel bender is a compact, energy-efficient machine that delivers unbeatable productivity and flexibility while taking up minimal space in factories. Designed to enhance manufacturing capabilities, the P2 automatically produces a wide variety of metal parts, adapting to different strategies like lean manufacturing, batch production, kit assembly, or single part flow. Experience the versatility and intelligence of the most productive Salvagnini panel bender, ever, and discover what it's like to work smarter with the P2!
(The P-ROBOT is available for this model.)
Product overview
The P2 uses universal bending tools which automatically adapt in-cycle to the panel geometry, without machine down times or manual retooling, allowing batch-one or kit productions.
The technical solutions adopted (Direct Drive and pneumatic and electric actuators) allow the P2 to respect both people and the environment without reducing its productivity. The P2 runs with a minimum quantity of long-life oil, inside a fully sealed circuit.
The integrated adaptive technologies (advanced sensors, bending formula, MAC3.0) make the system intelligent and able to automatically adapt to changes in the material and the external environment, eliminating waste and corrections, and extending the range of products that can be made.
The proprietary LINKS, STREAM and OPS softwares establish communication between the system and the company departments involved in the production flow.
The P2 offers customized solutions, including auxiliary tools and additional devices for special geometries or different loading/unloading solutions with additional door (PIN2) or robot (PIN3).
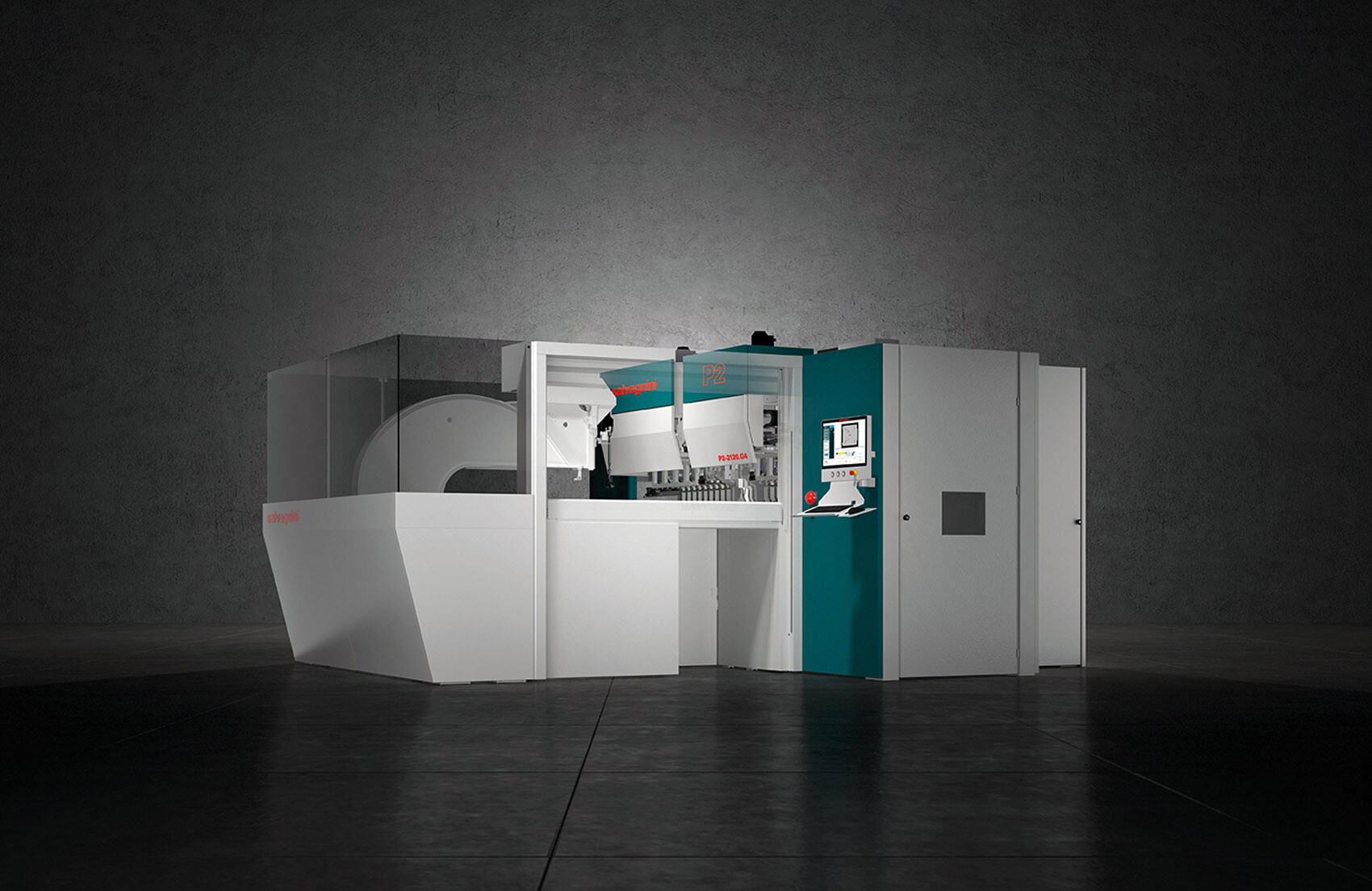
Discover How the P2 Is Right for You
MAC3.0
MAC3.0 detects any differences in the mechanical characteristics of the material compared to their nominal value during the cycle, adapting the movements of the bending unit and the manipulator to compensate them.
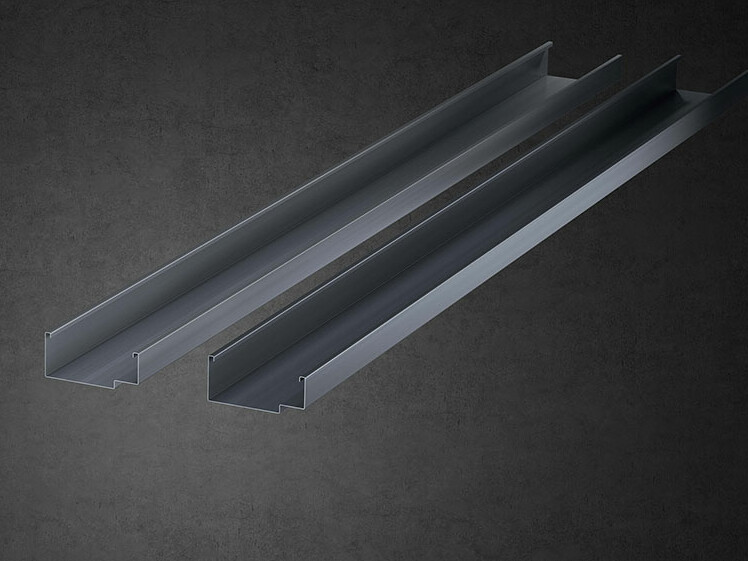
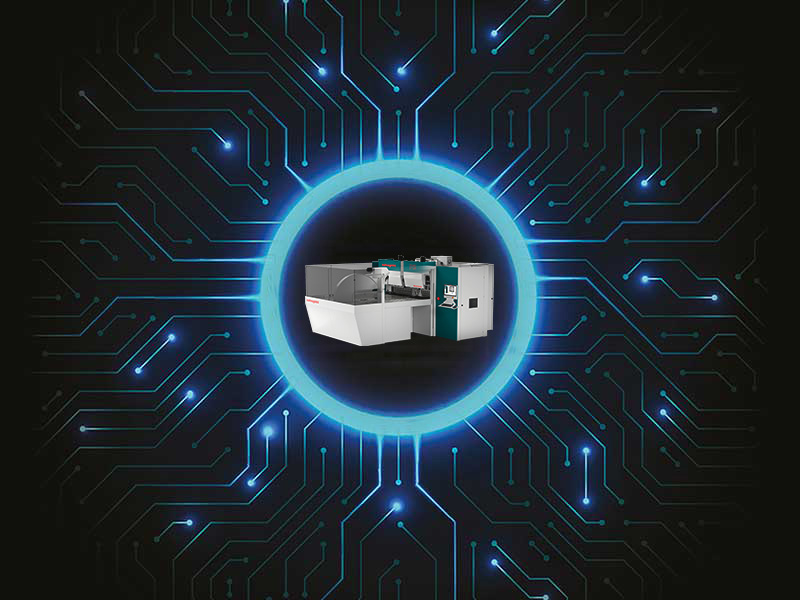
Industry 4.0
Digital transformation and Industry 4.0 are key topics for staying competitive on the market. When adopted, they can implement and manage complex, integrated, highly automated high-performance systems, and can help to develop simple solutions that require no structural changes to the production layout, making the world of smart manufacturing much more accessible.
Intelligent system, constant quality
Practically everything you ever wanted to know about the P2 panel bender, satisfactorily explained.
Conventional bending is characterized by an average OEE of 30%, with flexibility dependent on the tool change system - which is often costly and more time-consuming than on a panel bender - or on the installation of more than one press brake. The P2 panel bender, on the other hand, natively combines productivity, with its automatic bending and handling cycles, and flexibility, with its universal bending tools. And with its advanced cycles, the P2 completes an average of 17 bends per minute
The P2 doesn’t require re-tooling: the upper and lower blades, the counterblade and the blankholder are universal tools that are able to process the whole range of thicknesses and machinable materials.
Loading and unloading are performed by the operator, who positions the sheet metal on the worktable and collects the product after bending. The P2's cycle minimizes the impact of these activities on total cycle time, as it allows the product to be unloaded after positioning the sheet on the worktable, thus combining two operations in a single action.
The set-up has minimal impact on the panel bender's productivity: when the program is loaded, the blankholder automatically adapts in masked time, and the manipulator gets into position for gripping and handling the sheet.
The P2 is equipped with an automatic blankholder, which automatically adapts the length of the tool according to the size of the part to be produced, without the need for machine downtime or manual re-tooling even in-cycle: the ideal solution for batch-one and kit production.
MAC3.0 is the set of integrated technologies – sensors, formulas and algorithms – that make the panel bender intelligent: it eliminates waste and reduces corrections, measuring in-cycle and automatically compensating any variability in the material being machined.
The P2 integrates advanced sensors that measure the actual thickness and effective size of the part to be machined, and detects any deformations caused by variations in temperature. The data are fed in real time into the bending formula, which defines the correct force to apply to the sheet metal, guaranteeing the precision, repeatability and quality of the finished product.
In addition to the automatic ABA blankholder, the P2 offers a range of options to guarantee maximum versatility and adaptability, to suit any production strategy or mix.
The P2 can be equipped with proprietary OPS software, which ensures communication between the panel bender and the factory ERP: depending on needs, OPS manages the production of sequences of different parts. Universal bending tools, automatic in-cycle set-up and automatic handling allow the system to respond to any requests immediately.
The sheet metal is centered, just once at the start of the process, against controlled reference stops: this minimizes the cycle time as well as any precision errors, which are all absorbed by the first bend. The bending formula automatically optimizes the bending parameters to reduce waste, while MAC3.0 detects and automatically compensates any variability in the material to guarantee precise, high-quality bends.
Software
Industry has changed: flexibility and efficiency are fundamental requirements for managing increasingly smaller batches or rapid item turnover rate. And developments in technology have in some way upset the balance between workloads, with increasingly fast systems which however need to be guided by more and more specific machine programs, the generation of which is increasingly time-consuming. This is why software is increasingly crucial to improving the efficiency of machinery.
Salvagnini’s IoT solution, increases the global efficiency of the panel bender. LINKS allows real-time monitoring of the machine’s performance and independent analysis.
Technical data
Model | P2-1620 | P2-2120 | P2-2226 | P2-2520 | P2-2720 | |
Maximum length of incoming sheet (mm) | 1995 | 2495 | 2815 | 2795 | 3050 | |
Maximum width of incoming sheet (mm) | 1414 | 1600 | 1600 | 1600 | 1600 | |
Maximum diagonal that can be rotated (mm) | 2000 | 2500 | 2820 | 3200 | 3200 | |
Maximum bending force (kN) | 240 | 330 | 590 | 660 | 660 | |
Maximum clamping force (kN) | 380 | 530 | 635 | 1060 | 1060 | |
Maximum bending length (mm) | 400-1000 | 1000-1600 | 2180 | 2200 | 2500 | 2750 |
Maximum bending height (mm) | 203 | 203 | 260 | 203 | 203 | |
Minimum thickness (mm) | 0.4 | 0.4 | 0.4 | 0.4 | 0.4 | |
Maximum thickness and bending angle steel, UTS 410 N/mm2 (mm) | 3.2 (±90°) | 2.5 (±90°) | 3.2 (±90°) | 3.2 (±90°) | 3.2 (±90°) | 3.2 (±90°) |
Maximum thickness and bending angle stainless steel, UTS 660 N/mm2 (mm) | 2.5 (±90°) | 2.1 (±90°) | 2.5 (±90°) | 2.5 (±90°) | 2.5 (±90°) | 2.5 (±90°) |
Maximum thickness and bending angle aluminium, UTS 265 N/mm2 (mm) | 3.5 (±120°) | 3.2 (±120°) | 4.0 (±120°) | 4.0 (±120°) | 4.0 (±120°) | 4.0 (±120°) |
Average absorbed power (kW) | 3.0 | 3.0 | 4.0 | 5.0 | 5.0 | |
Noise level (Machine Directive 2006/42/EC) (dB) | 68 | 68 | 68 | 69 | 69 |
Values refer to a standard machine. Salvagnini reserves the right to modify this data without warning.