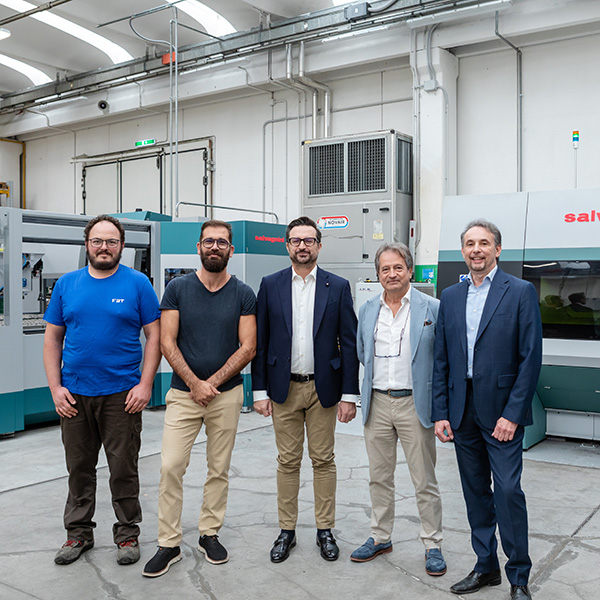
Insight
FBT Elettronica: Rethinks service to optimize the VAIE panel
Story courtesy of M.B. Mereu and S. Raimondi/Tecnolamiera
Rethinks is Salvagnini's service to help companies take on the day-to-day challenges imposed by the market by rethinking and redesigning their production to get the most from their systems.
Rethinks is a service exclusively for Salvagnini customers to help them exploit the potential of their systems for an even higher competitive position in the market. Rethinks connects customers with skilled Salvagnini specialists to optimize production process and improve quality and efficiency, reducing the number of work steps, material usage and costs. Rethinks includes two service options: a design course for designers and a part design support service.
The first option is a customized design course for designers. The goal is to work upstream to improve the knowledge of the specific technologies at the production site, enabling more efficient use of them. The design course provides designers with advanced skills.
The second is a design support service. The Salvagnini specialists place their own experience and skills at the disposal of the customer's designers, helping them to design or redesign their products. This is real expert support for the operational steps of component design, identifying the best solutions for each case to guarantee reduced waste and the optimization of the whole production process, even upstream and downstream of the Salvagnini technologies.
FBT Elettronica chose Rethinks
Mauro Senesi, Mechanical Designer at FBT Elettronica, explains the benefits achieved by using the Rethinks service for the redesign of the front panel of the EVAC VAIE evacuation system.
- Why redesign the product?
"We overhauled our machinery fleet, adding cutting-edge technologies such as the Salvagnini laser and panel bender. Following this investment, we decided to use the Rethinks service to re-industrialize part of the production for these technologies." - What's changed?
"From an aesthetic point of view, the front panel did not undergo any particular modifications. In compensation, its redesign considerably reduced the number of components: from three components and four stiffeners to just two components. What’s more, we moved from the punching and bending steps to laser cutting and panel bending. This optimization had a significant impact on the production process, because it reduced the processing stages required and eliminated sanding and spot welding." - What are the benefits?
"The most significant benefit was the reduced cycle time of the processing steps. Moving from a punching machine to a laser allowed us to reduce the cutting time by 20%, while the switch from traditional bending machine to panel bender reduced the bending time by 80%. As regards the optimization of the production process, the quality of the laser cutting on 1.5 mm galvanized sheet metal did not require any additional processing on the flaps allowing the sanding step to be eliminated. Redesigning the components for panel bending reduced the number of bends required by 50% and eliminated welding. The technology and process change did not require modification of the production management strategies, which retained the same logic and minimum batch sizes. Making use of the laser increased efficiency in the use of the sheet metal: on average, our current nestings have reduced waste by 20% compared to the past. A further benefit regards the cost of the component, which has fallen by around 20%."