Punch-laser machine
The S1 is a true work center that punches, forms, taps, cuts and separates the parts. It optimizes the production process, reducing waste, minimizing intermediate handling and operator intervention.
A cutting-edge solution
S1 is a punch-laser combi machine, a true work center that punches, forms, taps, and cuts parts.
Product overview
The S1 laser punching machine maximizes process efficiency: all the punching, forming and separation operations are automatic, done by a single system that eliminates semi-finished parts, does not require manual intervention and assures extreme repeatability.
The store-towers and automatic loading/unloading devices increase the autonomy of the system, making it possible to select from among various strategies:
• production of single parts;
• production of multiple parts and nests, microjointed or separated, with preservation of the scrap and unloading of the skeleton;
• production of multiple parts and separated nests, with destruction of the skeleton.
The integrated adaptive technologies make the system intelligent and able to automatically adapt to variations, eliminating waste and corrections, while guaranteeing high machining quality:
• the centering control system measures the incoming sheet and adapts the program to the actual dimensions measured, if necessary;
• the two-carriage manipulator changes its dynamics based on the dimensions and weight of the sheet;
• an automatic system checks the thermal expansion of the manipulator’s axes and compensates any variations, guaranteeing extreme positioning precision;
• the tool movement drive with controlled descent reduces cycle times and improves punching quality.
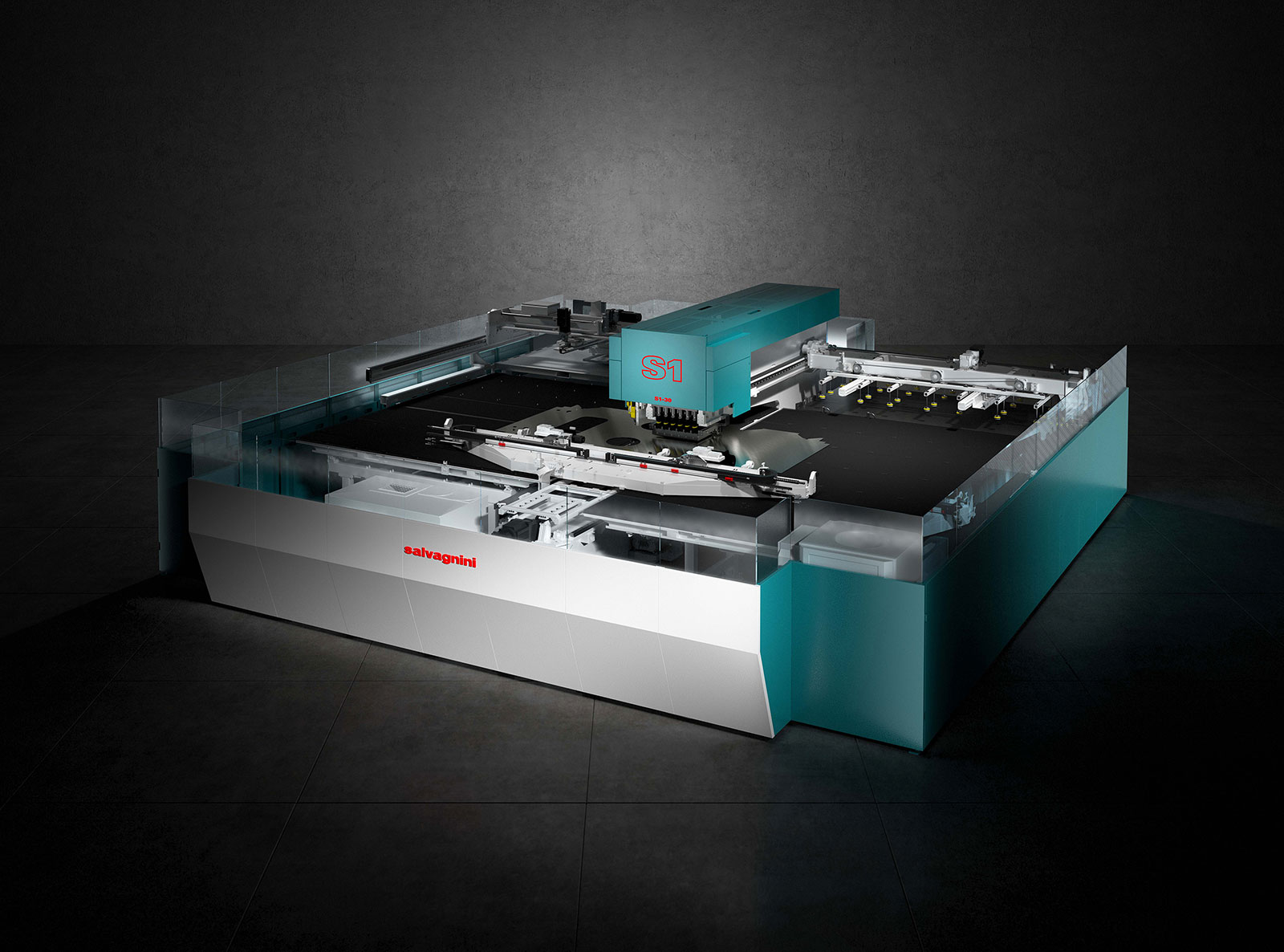
Industry 4.0
Digital transformation and Industry 4.0 are key topics for staying competitive on the market. When adopted, they can implement and manage complex, integrated, highly automated high-performance systems, and can help to develop simple solutions that require no structural changes to the production layout, making the world of smart manufacturing much more accessible.
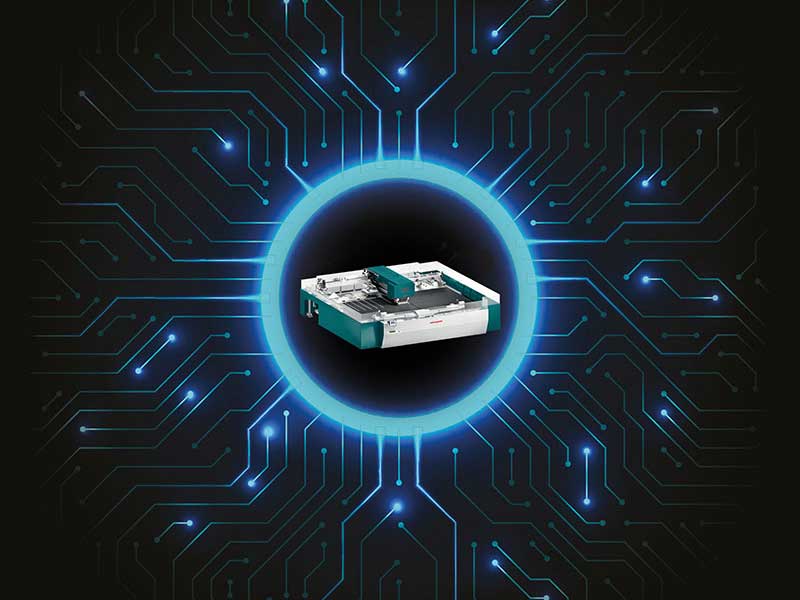
Intelligent system, constant quality
Practically everything you ever wanted to know about the S1 punch-laser combi machine, satisfactorily explained.
Today companies have to cope with many challenges in order to remain competitive in a continuously developing market. These challenges include:
- The need to automate information distribution, in order to create a lean, error-proof production environment, by integrating company ERP/MRP systems with process software for production management.
- The growing need to increase the autonomy and efficiency of production systems by automating loading, unloading and sorting operations.
- Finally, to prevent programming from becoming a bottleneck for production, the aim of implementing simple and quick office software solutions, able to make procedures leaner and improve overall efficiency.
For Salvagnini, punching is always a combined process of forming and separating parts, with the separation done either by shear or by laser. Part separation allows the punching machine to be integrated in a modern and efficient production flow.
Part geometries, machinings necessary, increasingly small batch sizes, cutting quality, reduced consumption and expected productivity are factors that make the S1 an attractive investment.
Productivity is guaranteed because the S1 is a single work center, able to automatically produce finished parts without the need for regripping and/or re-tooling.
The S1 integrates the punching and cutting operations and automatically manages repositioning and separation. With the patented multi-press head, the tools are always available for nesting and multiple jobs, with no re-tooling in-cycle or manual intervention. The controlled stroke of the tools, it extends the range of machinings available, including offset, ribbing and tapping.
With conventional punching, productivity and flexibility depend on the number of tool changes in-cycle and the times for moving the sheet underneath the turret or single punch, influenced by the time required for the sorting operations downstream. The S1, on the other hand, natively combines productivity and flexibility. Productivity is maximized by the multi-press head with evolved hybrid technology, which makes the tools always available, and the two-carriage manipulator with variable set-up which guarantees maximum sheet reachability. These unique solutions also improve the flexibility of the S1 as – whatever the geometries and materials being machined – they do not require e-tooling and can produce large batches, kits or batch one with equal ease. STREAM.COMBI, the programming software for generating the punching and cutting program, includes proprietary algorithms for optimizing nests and parts, while reducing scrap and improving performance. STREAM.COMBI makes it easy to choose the best production strategy, and simplifies the programmer’s job with a simple and immediate user-interface and its automatic programming, interactive work process editing and simulation functions.
The multi-press head requires no re-tooling or tool changes in-cycle, reducing overall processing times. The multi-press head is a distinctive feature of the S1 and can house up to 59 tools at the same time. It ensures high punch-die alignment precision, for high-quality machining. The head configuration proposed for each customer is designed to meet their specific production needs, and to minimize tool changes which, when required, are simple and very quick.
The different S1 loading/unloading solutions and the evolved programming respond to different production needs.
Production of single parts, multiple parts and nests with scrap preservation to:
• reduce production times;
• simplify programming activities.
Production of single parts, multiple parts and nests with scrap destruction to:
• ensure flow processing, in line;
• reduce scrap.
In its basic configuration, the S1 is a semi-automatic solution: the operator loads the sheet manually on the worktable and then unloads it once processing is complete. The manipulator automatically manages all repositioning, with extreme precision, during the entire work cycle.
Salvagnini offers feeding and unloading solutions with an increasing level of automation that permits unmanned processing by optimizing each single work phase and promoting the in-line or in-system integration of multi-technology processing.
The S1 is not a punching machine with cutting function, nor is it a laser, but it is a combination of two different technologies with the addition of advanced cycles, guaranteeing the optimization of workpiece movements. It is the parts to be produced, their geometries, materials, thicknesses, the machinings necessary and the levels of productivity required, that determine the choice of the most suitable technology and automation solution: the decision to choose the S1 must be evaluated on the basis of these criteria.
In addition to solutions that optimize the efficiency of each operation, Salvagnini supplies automation and process software which, by suitably organizing the whole production flow, help to achieve greater autonomy for unmanned and lights-out jobs, reducing the impact of labor costs and the return-on-investment time.
Salvagnini supplies a wide range of store-towers and automatic loading/unloading/sorting devices which, when coupled together, increase system autonomy and efficiency. These devices mean that different materials and thicknesses are always available for just-in-time jobs, minimizing waiting times for sheet metal feeding and reducing the risk of error or damage to the material resulting from human intervention. These are modular and customizable solutions that can be extended and/or modified even after they are first installed.
The S1 is available in two sizes, for machining 3 or 4 meter sheets. Both models can be configured by selecting from among the numerous loading/unloading automations. The model is chosen on the basis of an in-depth feasibility study. Salvagnini’s specialists help each customer to define the most suitable configuration for their production needs, evaluating a number of variables including the field of application, the production strategy and the production mix.
The S1 is available in two sizes, for machining 3 or 4 meter sheets. Both models can be configured by selecting from among the numerous loading/unloading automations. The model is chosen on the basis of an in-depth feasibility study. Salvagnini’s specialists help each customer to define the most suitable configuration for their production needs, evaluating a number of variables including the field of application, the production strategy and the production mix.
Software
Industry has changed: flexibility and efficiency are fundamental requirements for managing increasingly smaller batches or rapid item turnover rate. And developments in technology have in some way upset the balance between workloads, with increasingly fast systems which however need to be guided by more and more specific machine programs, the generation of which is increasingly time-consuming. This is why software is increasingly crucial to improving the efficiency of machinery.
Salvagnini’s IoT solution, increases the global efficiency of the punching machine. LINKS allows real-time monitoring of the machine’s performance and independent analysis.
Technical data
Model | S1.30 | S1.40 |
Maximum sheet dimensions (mm) | 3048 x 1524 | 4064 x 1524 |
Minimum sheet dimensions (mm) | 370 x 300 | 370 x 300 |
Punching | Laser cutting | |
Technology | Multi-press head | Fiber laser |
Source power (W) | - | 2000-3000 |
Assist gas | - | Nitrogen, compressed air |
Maximum material thickness (mm) |
| |
Aluminum, UTS 265 N/mm2 | 5.0 | 5.0 |
Steel, UTS 410 N/mm2 | 5.0 | 5.0 |
Stainless steel, UTS 660 N/mm2 | 5.0 | 5.0 |
Minimum material thickness (mm) | 0.5 | 0.5 |