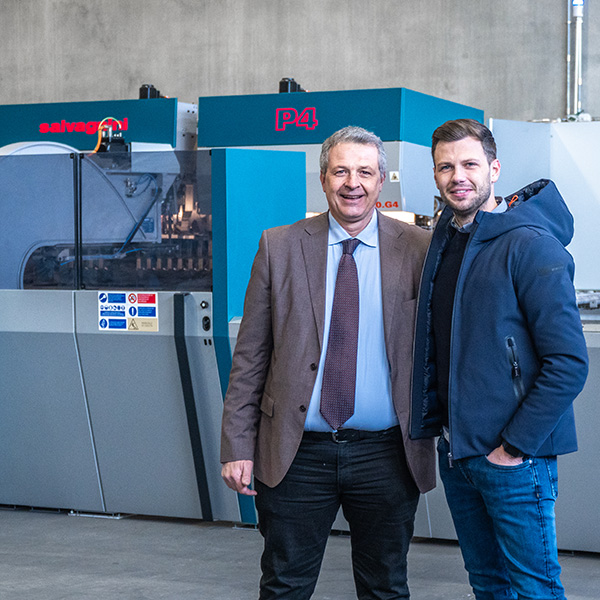
Case study
Officine Tironi: always ready to innovate, in-house too!
In four years of business, Officine Tironi has grown rapidly, increasing and optimizing its production of electrical boxes for transformers with its high-impact Salvagnini-branded technologies: from the L5 revolution for laser cutting with compressed air to the complete redesign of the production cycle to exploit the performance and automations of a P4 panel bending system to the full.
Always ready to innovate, in-house too!
Highlights
- Officine Tironi
Officine Tironi was founded in 2021 by Nicola Tironi, who built on extensive experience gained in the family business, Carpenteria Tironi. With a well-established presence in the mechanical industry in the Bergamo area, Officine Tironi stands out as a reliable and highly professional partner that offers design, fabrication, machining, and maintenance services for both light and heavy metal carpentry structures. The company covers a surface area of 10,000 square meters indoors, and employs 60 people, with a turnover that reached €7 million in 2024. - The context
Officine Tironi works in two main production sectors: electrical boxes for transformers, which are thin sheet metal boxes, and metalworks for industrial machinery. Electric box production has grown rapidly: from 20-30 boxes per month four years ago, today the company can produce around 140 a month, with ever-increasing demand. At the same time, Officine Tironi continues to maintain a strong presence in industrial metalworking, producing structures for the food, Oil & Gas and other industrial applications. One key aspect of the success of Officine Tironi is its constant attention to technical details and product quality. - The project
The arrival of the Salvagnini L5 6 kW laser cutting system marked the start of a radical technological change in Officine Tironi as the Salvagnini machine, with the ACUT option, is used to cut with appropriately treated compressed air. Thanks to it, the company has the same result as cutting with nitrogen, but with no gas costs. In terms of machined volumes, the increase has been dramatic: about 90% of the sheet metal is cut in compressed air. In addition, the company has implemented advanced programming systems, integrating Industry 4.0 to manage and program the machines directly from the technical department. Investments in automation have made it possible to organize the work over several shifts, two manned and one unmanned, when the systems run autonomously. Another targeted investment was the installation, in late 2024, of a Salvagnini P4-2520 panel bender with CLA tools to bend upward or downward tabs, and the CUT option for automatic and sequential profile shearing. An investment not only in the purchase of machinery but also in the full redefinition of the production process, with tangible advantages in terms of product quality and resource optimization. The introduction of the P4-2520 panel bender was not an improvised operation, but the result of an in-depth feasibility study conducted together with the Salvagnini team. - The outcome
“If Officine Tironi had continued to cut with nitrogen without any automation,” Nicola Tironi confirms, “it would in any case have reached 140 boxes a month, but with smaller margins and less competitive potential on the market”. At the same time, the introduction of the Salvagnini panel bender revolutionized both the way of working and the quality of the finished product. One of the clearest benefits: a drastic reduction in bending times - over 80%!
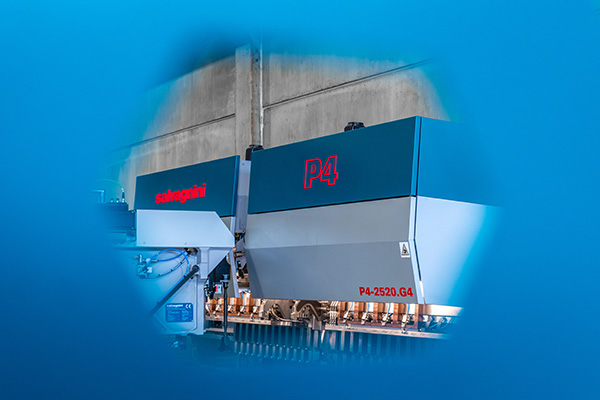