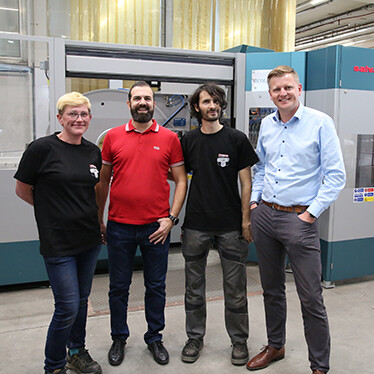
Case study
Even broader positioning thanks to panel bending
Story and pictures courtesy of N. Novotny/Blechtechnik
Due to considerable investments in the automation of press brakes, the subcontractor Terschl has been able to significantly increase its bending capacities over the past years. With the putting into service of a new Salvagnini’s P2, Terschl was able to develop further thanks to the introduction of the panel bending technology. This significantly increased their flexibility, capacity as well as their range of feasible parts.
Even broader positioning thanks to panel bending
Highlights
- Terschl
Terschl is synonymous with a variety of processes in sheet metal working. All the machining cycles of the tube, laser, punching, forming, and bending technology as well as the welding, chip removal and surface finishing can be carried out in Bad Hall in Upper Austria. - The project
Terschl's press brakes make a million bends a year. Four of the twelve press brakes are equipped with robots, and two of them also have automatic tool changers. But this Austrian company decided to invest in panel bending technology to offer added value to their customers. With panel bending, parts that are very difficult or even impossible to produce with a traditional press brake can be successfully processed. - The outcome
“The compact P2 was a perfect match for our needs. We could increase our output massively with the smallest possible footprint”, says CEO Werner Terschl. “Our manual and robotic press brakes are still a very important part of our production, as not all components in our product range are suitable for the P2. For the suitable parts, the panel bender is the perfect solution in terms of space. In fact, with the new panel bender the production/footprint ratio is 4:1 with respect to the press brake.”
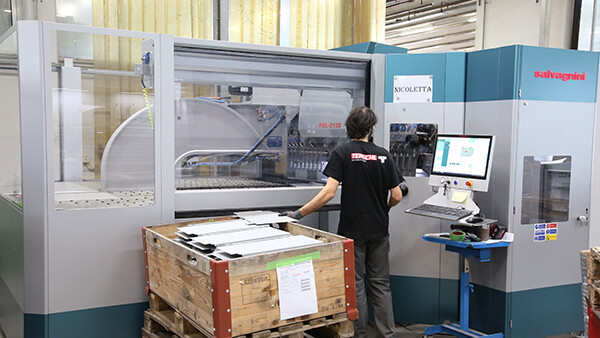
Check out the case study
Hear what Werner Terschl, Managing Director at Terschl, says about this project.