Fiber laser cutting machine L3: Adaptive fiber laser
The L3 is a versatile, multi-purpose laser designed for transversal use, whatever the applications, materials and thicknesses.
Product overview
Storage and automatic loading/unloading/sorting devices increase the autonomy of the system, regaining efficiency both in individual processing steps and throughout the production process, eliminating bottlenecks and reducing the impact of labor costs.
Proprietary functions such as TRADJUST, the simple and intuitive multi-interface, together with great accessibility, the portable terminal on board the machine, the artificial vision systems and the part tracing and identification solutions, allow operators to effortlessly solve any problems they come across in their day-to-day work, making the L3 agile and easy to use.
Advanced technical solutions, full control of the process with cutting-edge sensors, digitalization and the OPS software for real-time production management, eliminate low-added-value operations, zeroing downtime and reducing the cost per part, thus increasing factory performance.
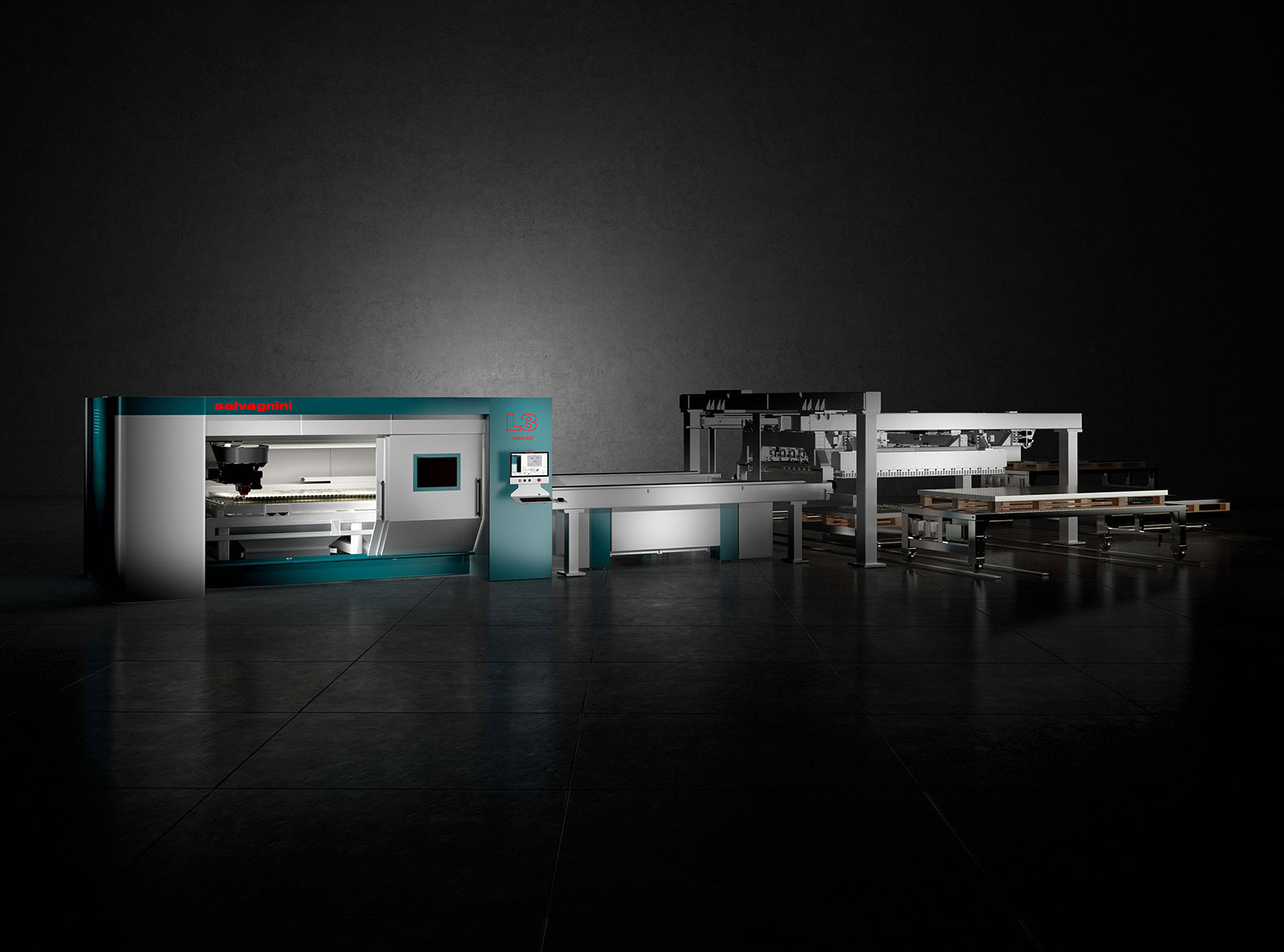
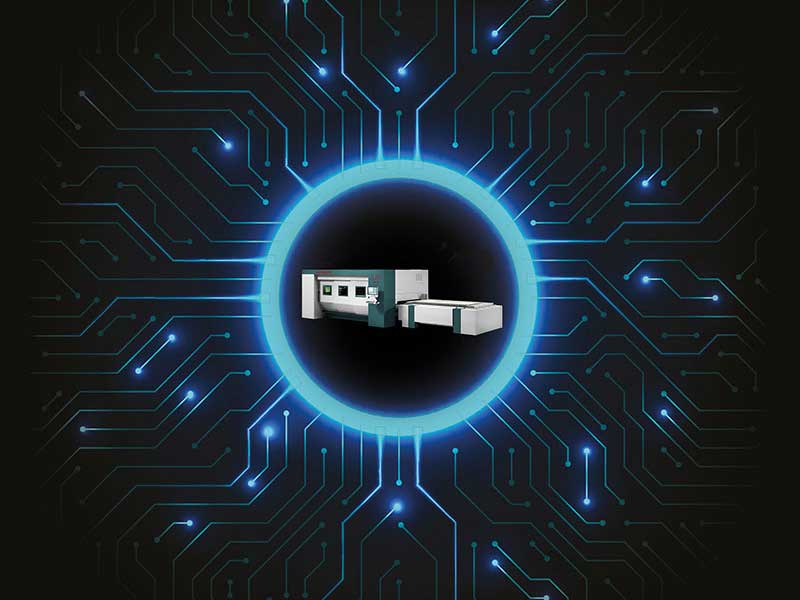
Industry 4.0
Digital transformation and Industry 4.0 are key topics for staying competitive on the market. When adopted, they can implement and manage complex, integrated, highly automated high-performance systems, and can help to develop simple solutions that require no structural changes to the production layout, making the world of smart manufacturing much more accessible.
In the laser world, automation is playing an increasingly key role: on the one hand, cutting speeds risk turning loading and unloading into bottlenecks, and on the other hand, automation can help to reduce the impact of labor costs. The loading/unloading and sorting connections satisfy all automation requirements: from stand-alone operation, to integration in flexible cells or in automatic lights-out factories.
Intelligent system, constant quality
Practically everything you ever wanted to know about the L3 fiber laser, satisfactorily explained.
The productivity of a laser is affected by market factors, i.e. everything the system cannot control, such as batch size, frequency of production changes and mix of materials/thicknesses; and by technological factors, which are linked to the features of the cutting system, such as source power, level of automation and digitalization.
The field of application, with its specific mix of materials, thicknesses and production strategies, is the key factor in the choice of technology: versatile and transversal, as in the case of the L3, or with high dynamics, like the L5.
Increasingly small batch sizes need rapid automation for rapid or masked-time production changes. Salvagnini offers a wide range of solutions: high-performance systems that are modular and compact for managing increased output, as well as systems that are open to downstream processes and designed to be effectively integrated into the factory’s production flow.
The range of thicknesses and the cutting performance depend on the power of the source. To meet different production needs, Salvagnini has introduced two sources: 6kW high-density and 10kW.
Efficiency and productivity are achieved by eliminating downtime, optimizing the process and simplifying the control system: these objectives can be reached with digital solutions that support the operator’s work and the OPS process software that manages the exchange of information with the ERP in real time and balances the production flow.
Increasing the productivity of a laser means guaranteeing efficiency throughout the whole process. The Salvagnini formula blends the power of the source with intelligent sensors and solutions integrated into the L3 laser, automation upstream and downstream of the cutting process, and digitalization. The result? Higher performance, and an optimized production process.
The L3 is equipped with a single laser head, designed by Salvagnini, used to cut all the allowed materials and thicknesses. It is equipped with the patented DRY-COOLING system, used to actively control the temperature of the optics. Its process sensors control and adapt the piercing in real time, monitoring any cutting losses, stopping the process, and restarting it with appropriately corrected parameters. The TRADJUST function, integrated into the proprietary control, ensures automatic parameter modulation according to the trajectories, making the system easier to use.
The market demands cutting-edge systems, with high performance, that are automated yet easy to use, manage and maintain. The L3 is an agile laser: the proprietary functions, the multitask human-machine interface and the artificial vision systems help operators to effortlessly solve the problems in their day-to-day work. Salvagnini software solutions effectively connect the laser to the factory ERP and other technologies downstream, guaranteeing the traceability of the parts, supporting the operator in sorting the parts and providing progress feedback in real time to the production manager, whether this is human or virtual.
The artificial vision systems implemented on the L3 simplify activities which require time or generate errors and waste. They are simple solutions that increase the flexibility of the system and broaden its field of application. AVS turns laser cutting into a work station downstream of punching, thus guaranteeing the maximum precision of the cut parts. SVS regains scrap and sheet metal leftovers, responding to urgent needs or replacing any waste in downstream machining activities. NVS checks that the laser beam is centered, and uses the machine learning algorithms to monitor the state of the nozzle and reduce waste.
It is the perfect combination: digitalization has led to the development of simple solutions, which have turned several traditional processes into smart production flows. OPS, the modular software for production management, receives the production list from the factory ERP/MRP in real time and supports the programming activities, defining priorities, rules and algorithms. OPS therefore helps to automate the process, adding intelligence to the system. The OPS applications for simplifying workshop management include PDD, which supports the operator via the monitor for manual part separation and sorting, and LPG, which laser-guides the operator in the pick-up sequence.
These challenges relate in particular to the recovery of autonomy and efficiency. Automating loading/unloading/sorting operations ensures improved cutting system performance and brings benefits to the whole production manufacturing chain. Implementing simple, quick office software reduces the risk of turning programming into the bottleneck of production. Integrating ERP/MRP and process software for managing production automates the distribution of information, helping to create a lean, error-proof production environment.
Automation plays an increasingly important role: the highest performing laser systems require loading/unloading/sorting devices that are equally high-performing. These solutions not only guarantee greater efficiency and autonomy for the systems they serve, they also reduce the impact of labor costs and the return-on-investment time.
The data from LINKS, the Salvagnini IoT solution, shows that the efficiency of a standalone laser system generally does not exceed 60%. This parameter varies with configuration: systems with automation have average efficiency values that are much higher, reaching 80% for horizontal loading/unloading solutions and even 90% if we consider the LTWS store-tower.
The minimum level of automation for the L3 laser is the CPE device, the ultra-rapid electrical pallet changer. The raw material always passes above the material that has already been cut, preventing any scrap from previous machining being deposited on the sheet metal.
The LTWS store-tower has automated loading/unloading, an enabling factor for increasing the autonomy of the cutting system. It ensures different materials and thicknesses are available for just-in-time production, reducing waiting times for sheet metal sourcing, and operator dependency. In contexts marked by low volumes and rapid production changes, LTWS is a winning choice.
The LTWS store-tower offers even greater performance when equipped with a sorting device: the automatic MCU or the manual TN. The store-tower manages different materials, thicknesses and sizes, reducing waiting times and making loading/unloading extremely fast: just 50 seconds. STORE, the store control software, is able to identify the loading trays, once emptied, as trays on which to stack the cut material, thus increasing operational autonomy.
Software
Industry has changed: flexibility and efficiency are fundamental requirements for managing increasingly smaller batches or rapid item turnover rate. And developments in technology have in some way upset the balance between workloads, with increasingly fast systems which however need to be guided by more and more specific machine programs, the generation of which is increasingly time-consuming. This is why software is increasingly crucial to improving the efficiency of machinery.
Salvagnini’s IoT solution, increases the global efficiency of the laser system. LINKS allows real-time monitoring of the machine’s performance and independent analysis.
Technical data
Models | L3-30 | L3-40 | L3-4020 | L3-6020 |
XY working range (mm) | 3048 x 1524 | 4064 x 1524 | 4064 x 2032 | 6096 x 2032 |
Z axis stroke (mm) | 100 | 100 | 100 | 100 |
Maximum XY speed (m/min) | 156 | 156 | 156 | 156 |
Precision1 | ||||
Position accuracy Pa | 0.08 | 0.08 | 0.08 | 0.08 |
Average position range Ps | 0.03 | 0.03 | 0.03 | 0.03 |
Fiber sources | 2000W | 3000W | 4000W | 6000W | 8000WE5 | 8000W | 10000W |
Cutting capacity (maximum thickness in mm)2 | |||||||
Steel | 15 | 20 | 20 | 25 | 25 | 25 | 25 |
Stainless steel | 10 | 12 | 15 | 20 | 25 | 25 | 30 |
Aluminum | 8 | 10 | 15 | 20 | 25 | 25 | 30 |
Copper | 5 | 8 | 8 | 8 | 10 | 10 | 10 |
Brass | 5 | 6 | 8 | 8 | 10 | 10 | 10 |
Minimum thickness (mm) | 0.5 | ||||||
Consumption (in kW) | |||||||
Maximum absorbed power (in kW)3 | 16 | 18 | 21 | 28 | 28 | 34 | 42 |
Average absorbed power (in kW)4 | 11 | 12 | 13 | 16 | 16 | 20 | 24 |
1 Measurement calculated according to VDI3441 on maximum axis lengths.
2 Cutting quality on limit thicknesses may depend on geometries required, material quality and system operating conditions. At limit values, burrs may be present on the lower edge of the cut. These values are for the Salvagnini reference materials.
3 Maximum absorbed power calculated on a system with standard configuration when cutting 3 reference sheets of mild steel with a thickness of 0.8-6 mm.
4 Average absorbed power calculated on a system with standard configuration when cutting 3 reference sheets of mild steel with a thickness of 0.8-6 mm.
5 High efficiency version.