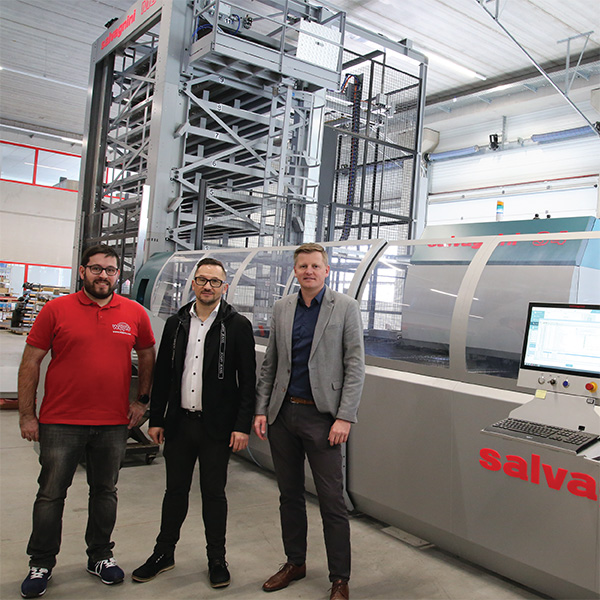
Case study
Wippro: fully automated with maximum flexibility
Story and pictures courtesy of N. Novotny/Blechtechnik
With the investment in a new Salvagnini S4 + P4 production line, Wippro GmbH, specialist in attic ladders and door systems, is paving the way for future success. Equipped with an upstream single-sheet store-tower and a stacking robot, sheet metal parts are punched, bent and optimally sorted for the following processes in a fully automatic manner.
Fully automated with maximum flexibility
Highlights
- Wippro
For more than 65 years, Wippro GmbH has been engaged in the design, development and production of attic stairs and flat roof exits made of steel. Its attic stairs are particularly durable and fulfill the highest damping and insulation values that go far beyond the required specifications. - The context
The production strategy, with a combined system from raw sheet up to the finished punched and bent steel part, has more than proven itself over a period of 25 years in Vorderweißenbach. The production line has provided an excellent service. Also the cooperation with Salvagnini, regardless for the supply of spare parts or technical support, has always worked smoothly in all these years. Ultimately, the extremely flexible and fully-automated production concept was the reason for which Wippro decided again for Salvagnini's S4+P4 production line. - The project
Based on Salvagnini‘s MD sheet metal store-tower, the S4 punching machine is fed automatically with single sheets from the rows of trays. Thanks to the multi-press punching head in combination with the angle shears, parts are individually punched and quickly transferred further within the line. Subsequently, the MCU device brought the parts into the correct position for the P4 panel bender and transferred to it. After bending, the robot takes the part and stacks it on one of the unloading pallets. - The outcome
This has opened up fully new production options also from a design point of view and has considerably increased the leeway of part design. The new line has made much smaller tolerances possible. This, in turn, means less waste. Furthermore, the nesting of programming software has been considerably improved, and the blanks can be used much better. The company CEO explains the striking difference in speed as compared to the old line based on an example:"On the new line, the same batch of a punched-bent part can be produced in 22 minutes, whereas we needed more than 1.5 hours on the old line.“
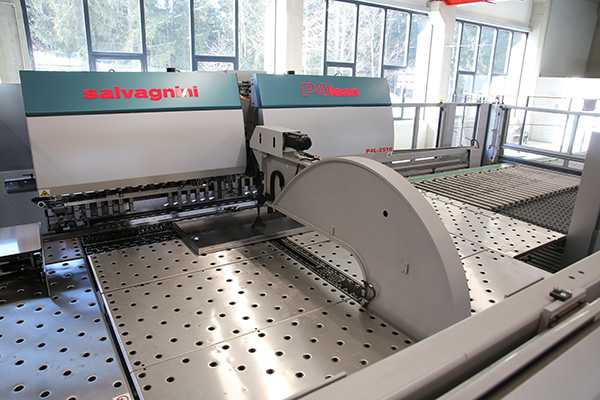
Check out the case study
Hear what Robert Wipplinger, CEO of Wippro GmbH, says about this project.