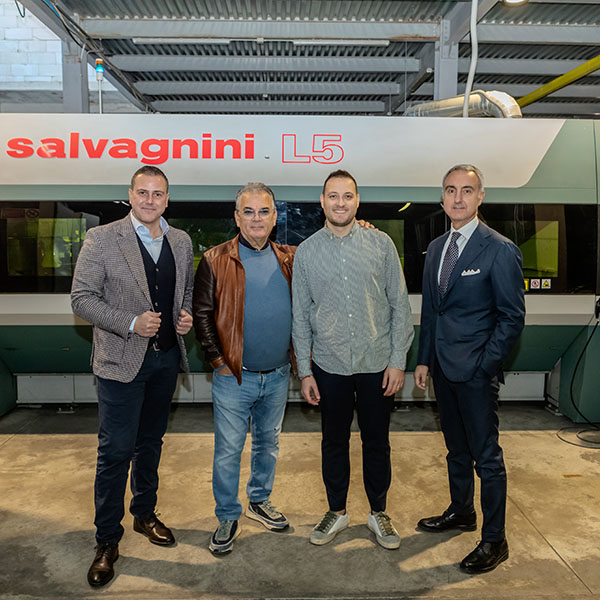
Case study
Ideam Inox: strength in automation
(and lots of benefits, too)
Story courtesy of E. Oldrati and L. Cantarelli/Deformazione
Specialized in processing of stainless steel for furnishing, Ideam Inox has, over the years, combined its growth with continuous regeneration of the production department, automating processes and integrating the different machines into a single production system. The key partner in this modernization has been Salvagnini, also providing consultancy for a redesign of the production flows which, thanks to its Concepts service, has led to a doubling of the Apulian company’s hourly production rate.
Strength in automation (and lots of benefits, too)
Highlights
- Ideam Inox
Currently, Ideam Inox brings together three different brands: Il Lattoniere, Puglia Inox and Lamiform Italia. Il Lattoniere is primarily engaged in the manufacture of extraction hoods and ventilation systems; Puglia Inox makes products for the laboratory fittings and furnishings sector; while Lamiform Italia makes furnishings for the bar/restaurant industry. The group has turnover of around 15 million Euros and is based in Grottaglie, in Italy's Apulia region, with total plant surface area of 45,000 sqm. - The context
The Apulian company's relationship with Salvagnini is long-standing. It all began in 2008 with the supply of a P4-2516 panel bender with HPT loading/unloading device, followed four years later by a 4 m, 2kW L3 stand-alone laser cutting system to meet new requirements dictated by an initial increase in production. The growth of Ideam Inox continues, always with the technological support of Salvagnini: in 2019, the machinery fleet was expanded with a new L5 laser and a new P4-3816 panel bender to increase the production capacity and bend parts up to 3850 mm long. - The project
Following Ideam Inox's request for a new P4 to further expand production capacity, the Salvagnini team put forward a new approach: it carried out an in-depth analysis of the production flows to understand how to best manage them, with the goal of combining an increased production capacity with a more efficient production process. These analyses led to the design of a new production layout which was very different from the original one, and significantly higher in terms of performance. A key role in this project was played by Concepts, Salvagnini's consultancy service which allows different production logic and flows to be studied to test out which system is the best suited to customer requirements. - The outcome
Thanks to in-depth simulations of Ideam Inox’s production, Salvagnini technicians have managed to define a workflow able to more than double the average hourly production capacity, which has indeed increased from 90 panels per hour to the current 180-200.
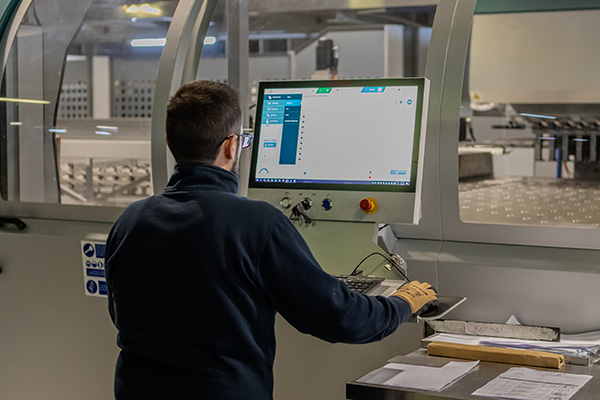