ハイダイナミックファイバーレーザー
L5は特に高性能なレーザーで、薄~中程度の板厚に対して高いダイナミクスを発揮します。
製品概要
保管および自動搬入/搬出/仕分け装置は、システムの自主性を高め、個々の処理ステップと生産工程全体の両方で効率を最大化し、ボトルネックを排除し、人件費の影響を軽減します。
コンパス駆動構造は、パーツ上の最適なポジションにおいて、高速かつ最小限のヘッド動作と精密な切断が求められる、ネスト切断に適したソリューションです。パラメーター調整、キネマティクス(動力システム)を制御する独自のアルゴリズム、完全なプロセス制御、先進センサーなどにより、全体的な効率が向上します。
シンプルで直感的なマルチタスクインターフェースであるTRADJUSTなどの独自機能は、優れたアクセシビリティ、機械本体に搭載されたポータブル端末、人工ビジョンシステム、パーツ追跡および識別ソリューションとともに、L5を迅速で使いやすいシステムにし、オペレーターが日常業務で遭遇する問題を簡単に解決できるようにします。
高度な技術ソリューション、最先端センサーによるプロセスの完全な制御、デジタル化、リアルタイムの生産管理のためのOPSソフトウェアにより、付加価値の低い作業が排除され、ダウンタイムがゼロになり、パーツあたりのコストが削減されるため、工場全体のパフォーマンスが向上します。
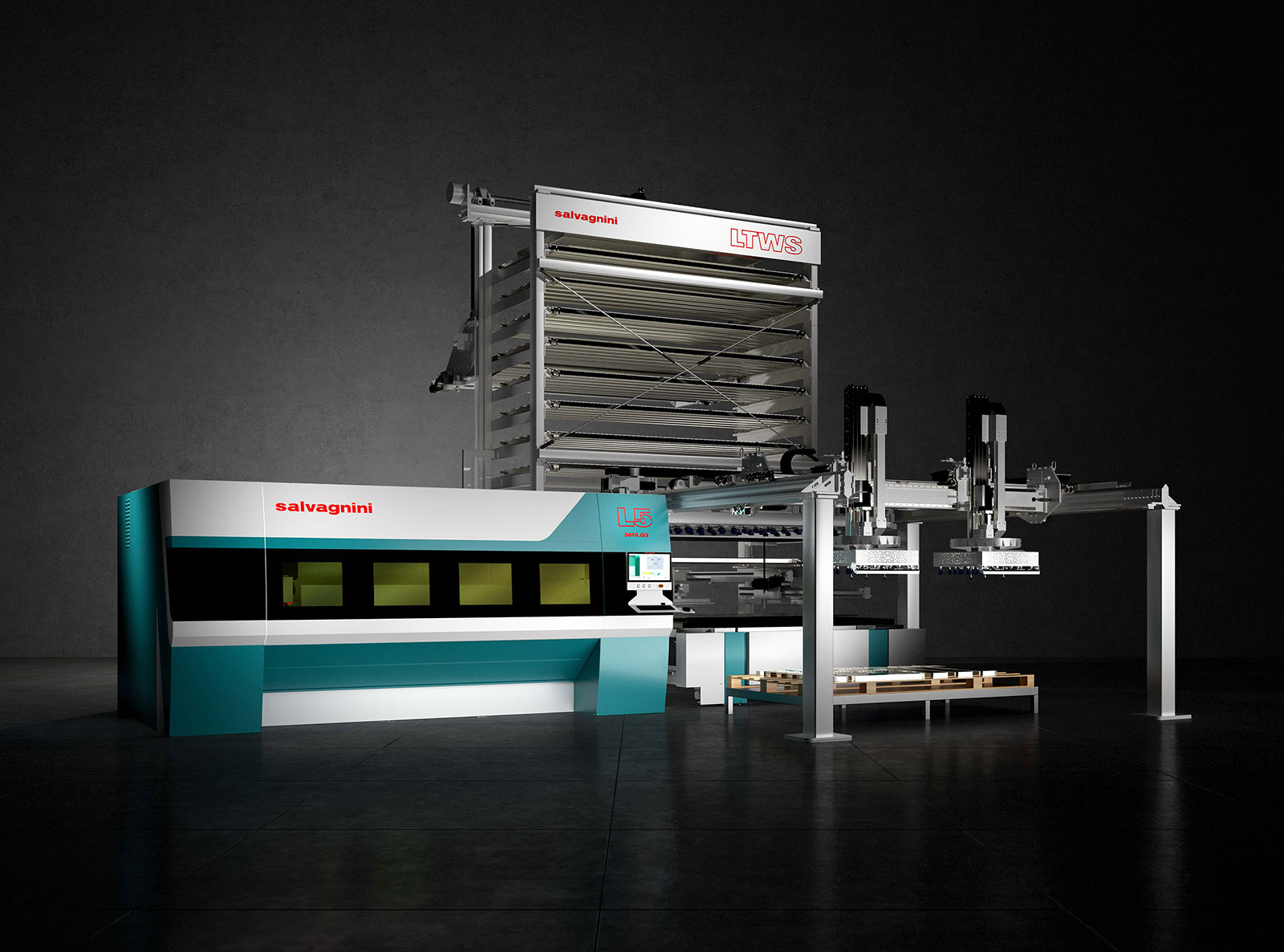
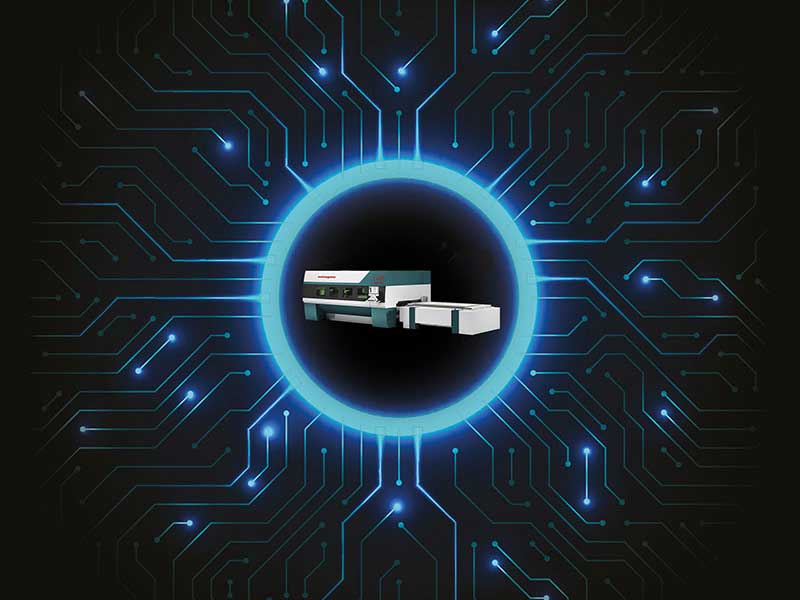
インダストリー4.0
デジタルトランスフォーメーションとインダストリー4.0は、市場での競争力を保つための重要なトピックです。これらを採用することで、複雑な統合された高度自動化高性能システムを実装および管理でき、生産レイアウトの構造変更を必要としないシンプルなソリューションの開発を支援して、スマートマニュファクチャリングの実現をはるかに容易にします。
レーザーの世界では、自動化がますます重要な役割を果たすようになっています。自動化は、搬入と搬出をボトルネックに変えるリスクがある一方で、他方では人件費の削減に大いに役立ちます。搬入/搬出と仕分け接続装置は、単体操作からフレキシブルセルまたは完全自動生産を行う工場でのインテグレーションまで、すべての自動化要件を満たします。
インテリジェントなシステムと均一な品質
L5ファイバーレーザーについて、お客様からよく頂く代表的な質問とその回答をまとめました。
レーザーの生産性は、市場要因、つまり、ロット数、生産変更の頻度、材料/板厚の混合など、システムが制御できないすべての要因から影響を受けます。また、発振源、自動化・デジタル化のレベルなど、カッティングシステムの機能に関連する技術的要因によっても影響を受けます。
材料、板厚、生産戦略の特定の組み合わせを利用した応用分野は、テクノロジーを選択する際の重要な要素です。L3の場合は汎用的で横断的であり、 L5の場合は高いダイナミクスを備えています。
ロット数がますます小さくなると、迅速な生産、または待ち時間なしの生産変更のために迅速な自動化が必要になります。サルバニーニは、出力の増加を管理するためのモジュール式でコンパクトな高性能システムから、下流工程に開放され、工場の生産フローに効果的に組み込まれるように設計されたシステムなど、幅広いソリューションを提供します。
板厚の範囲と切断性能は、発振源によって異なります。サルバニーニは、さまざまな生産ニーズに応えるため、6kWの高出力密度発振源と10kWの発振源を導入しました。
独自の機械システムであるコンパスは、リニアモーターを使用せずに最大5Gの加速度でレーザーヘッドを移動させることができ、消費電力を抑えながらシステムの生産性をさらに高めることができます。
効率性および生産性は、ダウンタイムの排除、プロセスの最適化、制御システムの簡素化によって達成されます。そしてこれらの目標は、オペレーターの作業をサポートするデジタルソリューションと、ERPとの情報通信をリアルタイムで管理し、生産フローのバランスを取るOPSプロセスソフトウェアによって実現可能になります。
レーザーの生産性を向上させることは、プロセス全体を通して高い効率を保証することを意味します。サルバニーニの公式は、ファイバーレーザー発振源と、L5レーザーに統合されたインテリジェントセンサーやソリューション、切断プロセスの上流と下流の自動化、およびデジタル化を融合しています。その結果、より高いパフォーマンスと最適化された生産プロセスを提供可能となりました。
L5には、サルバニーニによって自社設計された単一のレーザーヘッドが装備されており、機械加工制限内のすべての材料と板厚を切断するために使用します。これは高度なキネマティクス(動力システム)を備えたカーボンファイバー製のコンパスシステムに搭載されており、短い動きで最大5Gの動力でヘッドをXY平面上に動かします。特許取得済みのドライクーリングシステムを搭載しており、光学機器の温度を自発的に制御します。そのプロセスセンサーは、ピアッシングをリアルタイムで制御および適応し、カットロスを監視し、プロセスを停止し、適切に修正されたパラメーターでプロセスを再開します。独自の制御に統合されたTRADJUST機能は、軌道に応じて切断条件を自動的に調整し、システムをより簡単に使用できるようにします。
今日のレーザー市場は、自動化されていて、かつ簡単に使用でき、管理・保守も容易な高性能の最先端システムを求めています。L5はアジャイルレーザーです。独自の機能、マルチタスクヒューマンマシンインターフェース、および人工ビジョンシステムにより、オペレーターは日常業務で遭遇する問題を簡単に解決することができます。サルバニーニのソフトウェアソリューションは、レーザーを工場のERPやその他の下流のテクノロジーに効果的に接続し、パーツのトレーサビリティを実現し、オペレーターがパーツを仕分けするのをサポートし、人であるか仮想であるかにかかわらず、生産マネージャーにリアルタイムで進捗フィードバックを提供します。
L5に実装された人工ビジョンシステムによって、通常なら時間がかかる作業、またエラーや無駄が発生する作業を簡素化し、容易に行うことができます。サルバニーニのソフトウェアは、システムの柔軟性を高め、その応用分野を広げるシンプルなソリューションです。AVSは、レーザー切断をパンチングの下流のワークステーションに変えるため、切断加工後の素材の最高の精度を実現します。SVSは、スクラップや残材を再利用して、緊急の生産ニーズに対応したり、下流の機械加工作業で発生した廃棄物を交換することが出来ます。NVSは、レーザービームが中心にあることを確認し、機械学習アルゴリズムを使用してノズルの状態を監視し、無駄を減らします。
デジタル化はシンプルソリューションの開発につながり、それが従来のいくつもの加工工程をスマートな生産フローに変えました。つまり、デジタル化と簡素化は同時に実現できる完璧なコンビネーションです。生産管理用のモジュラーソフトウェアであるOPSは、工場のERP/MRPから生産リストをリアルタイムで受信し、プログラミング作業、そして生産順序・ルールおよびアルゴリズムの定義をサポートします。したがって、OPSは加工工程の自動化に役立ち、システムにインテリジェンスを追加します。ワークショップ管理を簡素化するためのOPSアプリケーションには、手動のパーツ分離と仕分けのためにモニターを介してオペレーターをサポートするPDD、およびピックアップシーケンスでオペレーターをレーザー誘導するLPGが含まれます。
これらの課題は、特に自主性と効率の最大化に関連しています。搬入/搬出/仕分け操作を自動化することで、カッティングシステムのパフォーマンスが向上し、製造工程全体に利益がもたらされます。シンプルで迅速なオフィスソフトウェアを実装することで、プログラミングが生産のボトルネックになるリスクが低減されます。ERP/MRPとプロセスソフトウェアを統合して生産環境を管理することで、情報配信が自動化され、無駄・誤差のない生産環境の構築に役立ちます。
自動化がますます重要な役割を果たします。最高性能のレーザーシステムには、同様に高性能なデバイスの搬入/搬出/仕分けが必要です。これらのソリューションは、レーザーシステムのより高い加工効率と自主性を実現するだけでなく、人件費と投資収益率の影響も軽減します。
サルバニーニのIoTソリューションであるLINKSのデータは、単体レーザーシステムの効率が一般的に60%を超えないことを示しています。このパラメーターは仕様によって異なります。自動化されたシステムの平均効率値ははるかに高く、水平方向の搬入/搬出ソリューションでは80%に達し、LTWS倉庫タワーを考慮すると90%にも達します。
L5レーザーの自動化の最小レベルは、超高速電気パレットチェンジャーであるCPEデバイスです。素材を載せているパレットは常に加工済みの材料の上を通過するため、切断加工で発生したスクラップが素材上に落下することがありません。自動化システムとの統合により、コンパス構造が持つ高い動力を最大限に活用して、極めて高い生産性と加工効率、および無人作業における高い信頼性を実現できます。
LTWS倉庫タワーは自動搬入/搬出が可能であり、カッティングシステムの自主性を高めます。これにより、様々な素材と板厚がジャストインタイム生産で利用できるようになり、素材調達の待機時間とオペレーターへの依存性が減少します。少量かつ急速な生産変更が特徴的な状況では、LTWSが勝利への最適な選択肢です。
LTWS倉庫タワーは、自動MCUまたは手動TNなどの仕分け装置を装備すると、さらに優れたパフォーマンスを発揮します。倉庫タワーは、様々な素材、板厚、サイズを管理し、待機時間を短縮し、搬入/搬出をわずか50秒と非常に高速化します。倉庫制御ソフトウェアであるSTOREは、空になった搬入トレイを、切断後の材料を載せる搬出トレイとして識別できるため、業務上の自主性が向上します。
技術データ
機種 | L5-30 | L5-40 |
XYワークテーブル (mm) | 3048 x 1524 | 4064 x 1524 |
Z軸ストローク (mm) | 100 | 100 |
XY 最大速度 (m/min) | 156 | 156 |
精度1 | ||
位置決め精度 Pa | 0.08 | 0.08 |
平均位置決め範囲 Ps | 0.03 | 0.03 |
ファイバーレーザー発振源 | 2000 W | 3000 W | 4000 W | 6000 W | 8000 WE5 | 8000 W | 10000 W |
切断板厚(mm)2 | |||||||
軟鋼 | 0.5 - 15 | 0.5 - 20 | 0.5 - 20 | 0.5 - 25 | 0.5 - 25 | 0.5 - 25 | 0.5 - 25 |
ステンレス | 0.5 - 10 | 0.5 - 12 | 0.5 - 15 | 0.5 - 20 | 0.5 - 25 | 0.5 - 25 | 0.5 - 30 |
アルミニウム | 0.5 - 8 | 0.5 - 10 | 0.5 - 15 | 0.5 - 20 | 0.5 - 25 | 0.5 - 25 | 0.5 - 30 |
銅 | 0.5 - 5 | 0.5 - 8 | 0.5 - 8 | 0.5 - 8 | 0.5 - 10 | 0.5 - 10 | 0.5 - 10 |
真鍮 | 0.5 - 5 | 0.5 - 6 | 0.5 - 8 | 0.5 - 8 | 0.5 - 10 | 0.5 - 10 | 0.5 - 10 |
最小板厚(mm) | 0.5 | ||||||
消費電力(kW) | |||||||
最大電力消費量(kW)3 | 16 | 18 | 21 | 28 | 28 | 34 | 42 |
平均電力消費量4 | 11 | 12 | 13 | 16 | 16 | 20 | 24 |
1 最大軸長時のVDI3441規格に従って計算しています。
2 限界板厚における切断品質は、必要とされる寸法、素材の品質、システムの運転状況に左右されます。限界値での切断においては、下側の端部分にバリが見られる場合があります。これらの値はサルバニーニ基準材料に対するものです。
3 板厚0.8〜6mmの軟鋼素材3枚を、標準設定のシステムで切断した場合に計算された最大電力消費量です。
4 板厚0.8〜6mmの軟鋼素材3枚を、標準設定のシステムで切断した場合に計算された平均電力消費量です。
5 高効率バージョン。