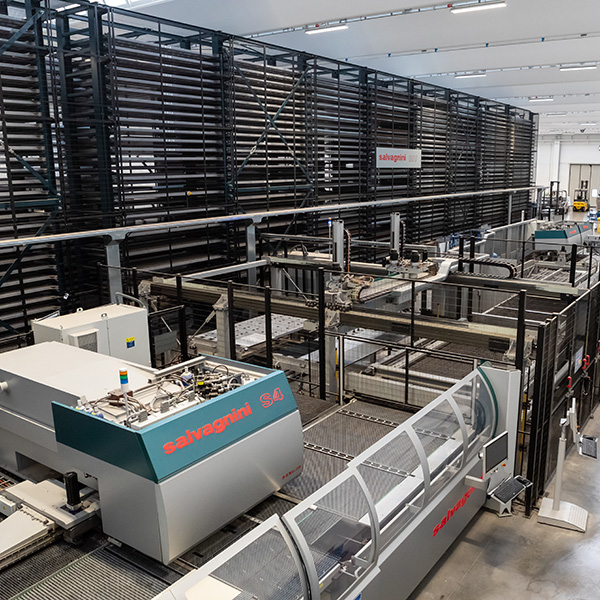
Case study
CMAlifts: a craftsman's heart, a 4.0 production
Story courtesy of E. Oldrati and G. Giannangeli/Deformazione
Looking to meet the global market, all processing steps must be automated, for both standard and high quality tailor-made products. To meet this goal in the elevator and lifting platform industry, CMAlifts has aimed for sheet metal working innovation and automation in a technological partnership with Salvagnini.
A craftsman's heart, a 4.0 production
Highlights
- CMAlifts
CMAlifts was founded in January 2001, based on an ambitious idea of the brothers Giulio and Gaetano Caputo. The company designs, manufactures and assembles homelifts, passenger lifts and elevators for civil and industrial use, including metal and mechanic shafts, cabins, as well as assemblies of complete systems. CMAlifts employs around 130 staff, and its headquarters are in Corato (Bari), with two production sites and a turnover of 42 million EUR per year. - The context
Gradually, in the last few years a latest-generation plant has been implemented, connected to the management system that interconnects all the company processes. The machinery used previously (guillotine shears, semi-automatic punching machines, manual press brakes) required excessive manual material handling, with low reactivity for just-in-time production and low competitiveness in the standard systems field. CMAlifts therefore had to overcome its low automation and optimize this production mix of small standard batches and working to order. - The project
The new plant was designed and implemented in collaboration with Salvagnini. The heart is certainly MV, a Salvagnini automatic double-row tray store with around 1000 positions: around 70 meters long, it can manage different sheet metal formats and connect all the individual technologies, harmonizing the machinery and optimizing all the steps. The MV feeds different technologies: two Salvagnini S4+P4 lines and three versatile Salvagnini 4-meter L3 fiber laser cutting systems. All the laser cutting systems are equipped with the ADLL automatic sheet metal loading-unloading device and an MCU device for automatic part sorting. At last, CMAlifts has taken another step forwards in its automation process, installing a Salvagnini ROBOformER robotic bending cell and connecting it to the plant. The whole plant is controlled by OPS, the Salvagnini software for real-time production management. - The outcome
CMAlifts has estimated that with the introduction of this plant, there will be a 30%-40% increase in production capacity and a 75% reduction in manual sheet metal handling: "The increase in production capacity has allowed us to further increase our customer portfolio and has led to a 10% increase in turnover," explain the Caputo brothers.
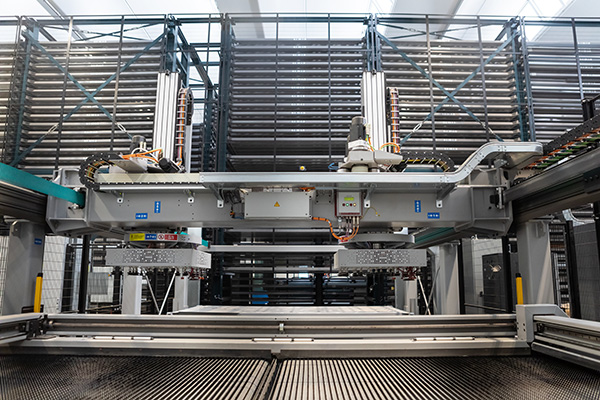