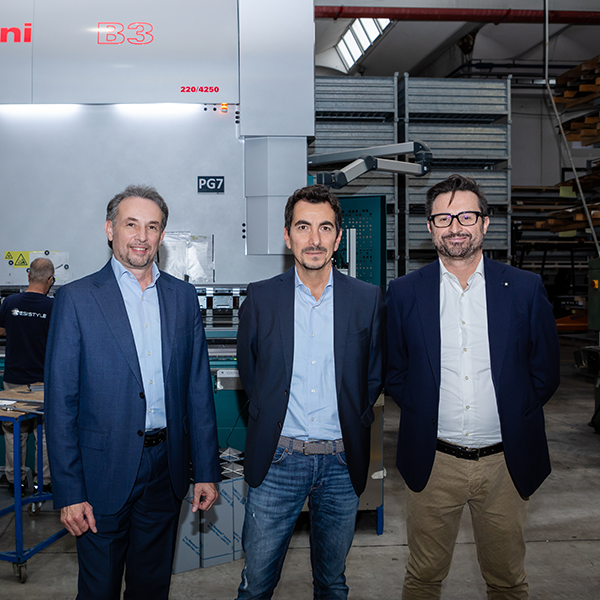
Case study
Esistyle: aiming for performance and flexibility for cooking in style
Story courtesy of A. Ariu and G. Mazzola/Lamiera
To meet new manufacturing needs, speed up time-to-market and increase competitive performance, Esistyle relies on Salvagnini technologies to manufacture cooker hoods, aspirating hobs and stainless steel kitchens with increasingly high aesthetics and functionality.
Aiming for performance and flexibility
Highlights
- Esistyle
Founded in 1981 as a subcontractor for the industries in Fabriano, the company began machining sheet metal for major, mostly local groups in the then-flourishing household appliance sector. In 2017, the shareholding structure and company name changed, from Metal Color to Esistyle. - The context
From 2017, Easistyle changed its core and production set-up, progressively accompanying the subcontracting activities with the design and production of an increasingly wide range of hoods and aspirating hobs, under its own brand as well as for private labels and OEM. This change required an upgrade of the layout. All the various manufacturing steps were reviewed in order to perform a complete product development cycle, up to final assembly. - The project
Precisely to meet a need for technological upgrading, Esistyle installed a new Salvagnini L5 fiber laser cutting system with a working range of up to 4,064 x 1,524 mm and a 3 kW source. The laser is fed by the ADLL automatic loading-unloading device, with its configuration that assures high machining precision even in the more aggressive cutting mode. One of the mandatory requests was for the machine to be able to perform laser cutting with compressed air, considering that the processed steel and stainless steel have thicknesses of between 0.8 and 5 mm. This possibility is offered by the ACUT option, which allows the Salvagnini lasers, depending on the source power, to cut thicknesses of up to 20 mm with appropriately treated compressed air, with productivity levels similar to those of cutting with nitrogen but with lower costs. The press brake chosen by Esistyle, on the other hand, is a B3 220/4250, which ensures 220 tons of force on a useful length of 4,250 mm, 3,620 mm distance between shoulders, 520 mm throat depth and a stroke of 450 mm. - The outcome
"Adopting Salvagnini technologies along with the digital transition allows us to efficiently coordinate every order today, with full traceability throughout all steps using barcodes, from the bill of materials to final assembly, including grinding and silking," explains David Lacchè, partner and managing director. "This means accelerating the time-to-market, transforming an idea into a finished product very quickly."
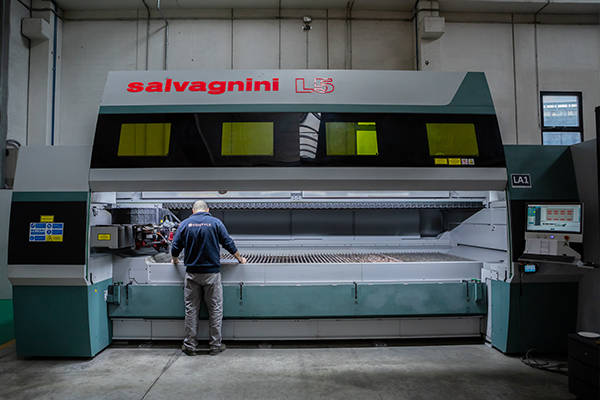