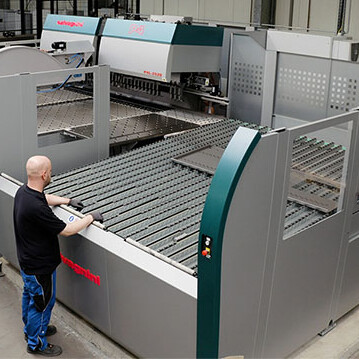
Case study
Henke: in the fast lane
Story and pictures courtesy of G. Maier/BLECH
In order to develop new areas of business, Henke GmbH was looking for a system that was optimally suited for kit production, but that also permitted low unit costs for large series thanks to a high production speed. With the Salvagnini S4 + P4 FMS, the company installed a system in 2021 that more than met their requirements.
In the fast lane
Highlights
- Henke
Henke GmbH is a specialist in industrial sheet metal processing from Altenstadt, Germany, equipped with the most modern fiber laser cutting systems, punching machines, press brakes, and panel benders. With approximately 125 employees, it processes more than 5000t of sheet metal per year. - The context
Henke GmbH started looking for alternative production options after the pandemic. A growing number of customers were looking for more flexibility in their provisioning, to be prepared for uncertainties in their supply chains. To meet this need and keep up with in-house production, especially in terms of price, Henke was looking for a solution that can cut, punch and bend sheet metal in a very flexible and fast manner, drastically reducing setup and idle times. - The project
With the S4 + P4 line, Henke GmbH found a flexible system that corresponded exactly to what it was looking for. Instead of feeding the punching machine from a single tray containing metal sheets with the same thickness, this system is able to pick individual blanks and, if necessary, also to feed the system with metal sheets of different thicknesses in sequence. While the system cuts and punches, the storage system preloads the next required metal sheet in masked time. Then it goes on with the punching: a tool change is not necessary here. With 96 integrated tools each with their own drive, the system is able to perform the different punchings required on a component almost at the same time, thanks to the multi-press punching head. - The outcome
It is therefore capable of separating and transferring the already punched component directly to the automatic panel bender while the other components are still being punched. Due to the elimination of setup times and waiting times, production can be sped up considerably.
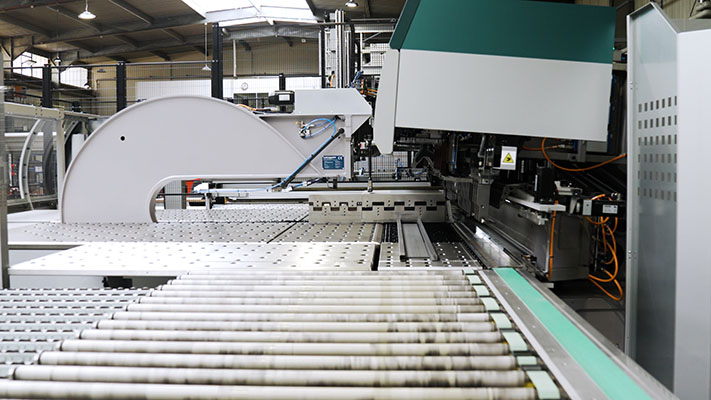
Check out the case study
Hear what Jens Wolf, Managing Director at Henke, says about this project.