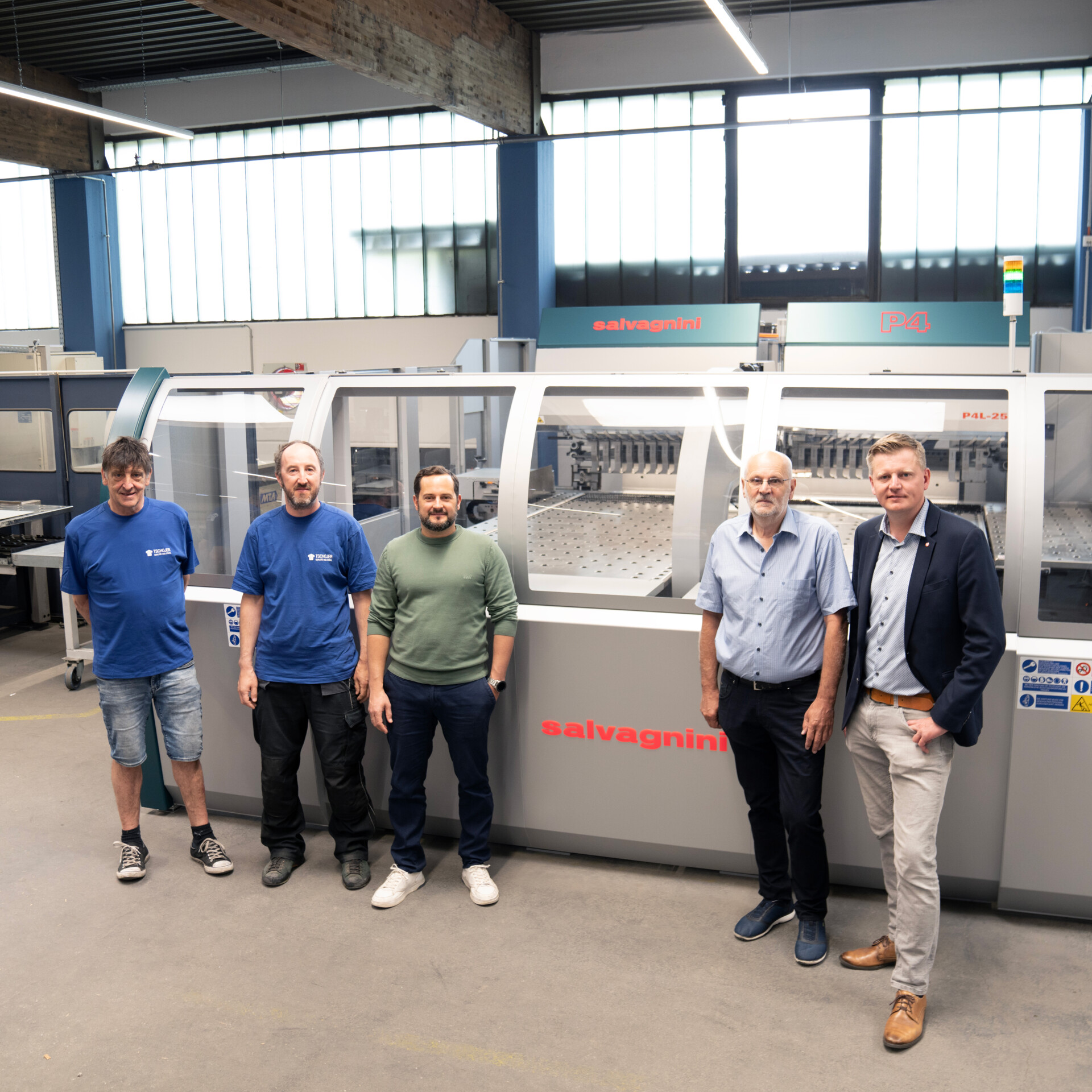
Case study
Melcher: 20 years after, 80% less consumption
Story courtesy of N. Novotny/Blechtechnik
The recent investment in a new Salvagnini P4 panel bender helped Melcher & Co – formerly known as Tschojer Quality Steel – increase production capacity while reducing cycle time and energy consumption.
20 years after, 80% less consumption
Highlights
- Melcher
Melcher & Co – formerly known as Tschojer Quality Steel – is a manufacturer of sheet metal furniture mainly for public swimming pools, hospitals, nursing homes and schools, although in recent years it has also increasingly opened up to the subcontractor market. Based in East Tyrol since 1983, the company is a family business now run by its third generation. Today, the company, which recently celebrated its 40th anniversary, has a total turnover of 10 million euros and about 200,000 production orders per year. The company processes around 1,400 tonnes of sheet metal per year, with a maximum thickness of 3 mm. - The context
Melcher has relied on Salvagnini technology since 2001. The company's main strengths are the customisation of products and the monitoring of their entire realisation. The entire production cycle is carried out in-house: has its powder coating, is able to manage certification processes and even fire safety tests. This allows Melcher to be the single point of contact for the customer and to have full visibility and control over the entire production process. - The project
In recent years the market requirements increased to an extent that automatic production with the old P4 was no longer viable. Melcher opted again for a stand-alone P4 panel bender with HPT, the automatic loading and unloading device. Choosing an extremely customized configuration has allowed the Austrian company to get work away from the press brakes and thus also to shorten the cycle times of the products. - The outcome
Melcher has increased productivity by around 18% and compared to the 2001 machine, the new P4 consumes 80% less electricity, significantly improving the company's overall CO2 balance. The benefits offered by digitalization are another advantage that stand out the new equipment: "Thanks to STREAM, the Salvagnini programming software suite, we have visibility, already in the quotation step, on how the components will be manufactured. In this way we can understand whether we will be able to manufacture them fully automatically and what the various production steps will be,” ends Tristan Tschojer.
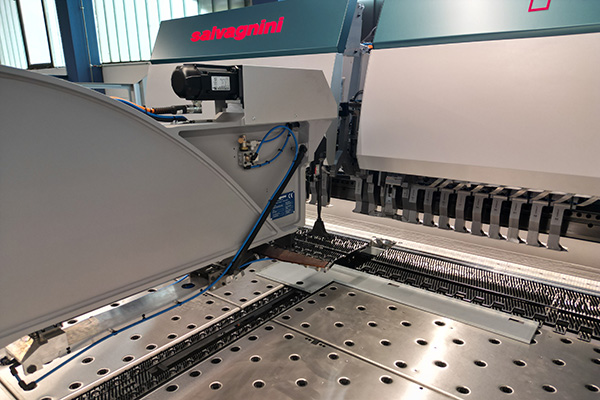
Check out the case study
Hear what Melcher & Co. executive team says about Salvagnini machinery.