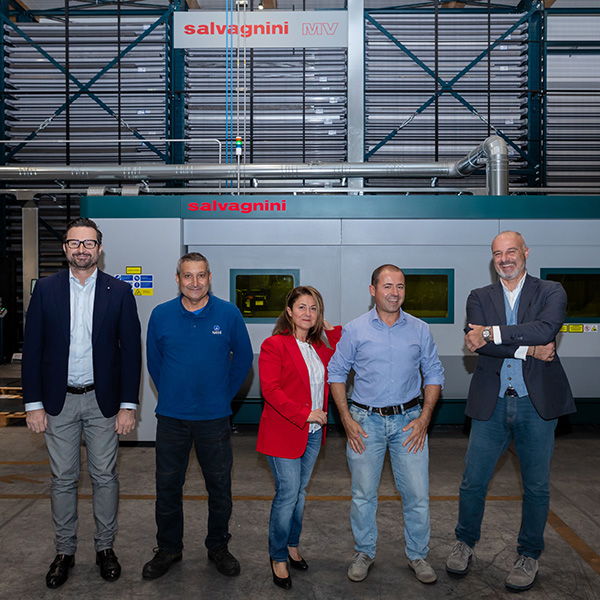
Case study
Nanni Ottavio: automation as an enabling factor for ensuring fast, precise production
Story courtesy of A. Ariu and G. Mazzola/Lamiera
Integrating automated systems and efficient, high-performing Salvagnini technologies has allowed Nanni Ottavio to optimize its production processes. The operational effect is reflected in better order management, faster and more precise processing and the ability to respond effectively to the demands of highly diversified customers, from small industries to multinational companies.
Automation as an enabling factor for ensuring fast, precise production
Highlights
- Nanni Ottavio
Founded in 1989, Nanni Ottavio works in a market with a large number of customers and highly fragmented orders, with highly complex management and organization. The company works to the customers’ designs, from the initial drawing to actual production, whether a simple part or a complete assembly. It manages over 40,000 order lines a year, offering solutions for a diverse range of final uses. - The context
The need to integrate new Salvagnini technologies comes from the precise need to cope with an increased cutting capacity, on larger sheet metal formats, and to facilitate the operators in sheet metal loading, unloading and especially sorting operations. - The project
Nanni Ottavio chose the Salvagnini L3 laser cutting system with adaptive fiber technology in the version with 10 kW source. The Romagna-based company was also very pleased with the Salvagnini MCU sorting device supplied with the laser cutting system, as this easily stacks parts with different shapes, sizes and weights. Another important part of the system supplied by Salvagnini is the 200 trays MV automatic tray store, designed for just-in-time production or batch ones, offering unmanned operation thanks to the high management autonomy of sheet metal, semi-finished and finished parts. - The outcome
"For us, the automatic tray store is not just a storage space but an active and decisive part of our production cycle. Our production is highly fragmented, with average batches of around 50 parts, and is planned on a weekly basis, when we cut all the materials and thicknesses in order. In this way, we can program a cutting step according to need, deciding on the best flow in relation to the delivery schedule. We are very flexible, we can decide to sort and group the cut parts by order, forwarding them to the downstream operations, place them on the trays or remove them from the production cycle if they are ready for delivery," says Nicola Nanni, the second generation at the helm of the business. The combination of the Salvagnini MV tray store and the MCU sorting device has assured significant floor space savings for the company, with the possibility to return the work-in-progress to the tray store and handle only the materials needed for the production in progress on the trolleys, minimizing low-value activities such as sorting, reducing sheet metal feeding waiting times and the risk of error or damage to the material.
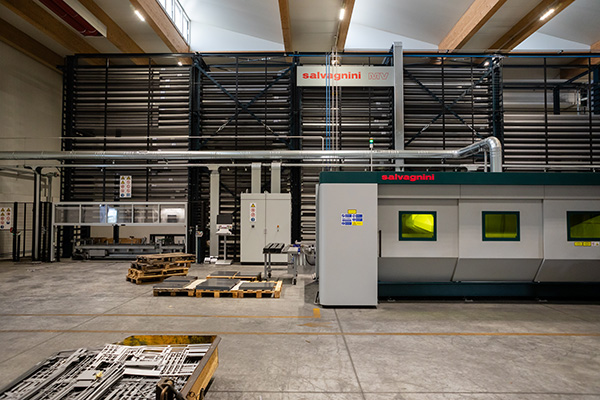