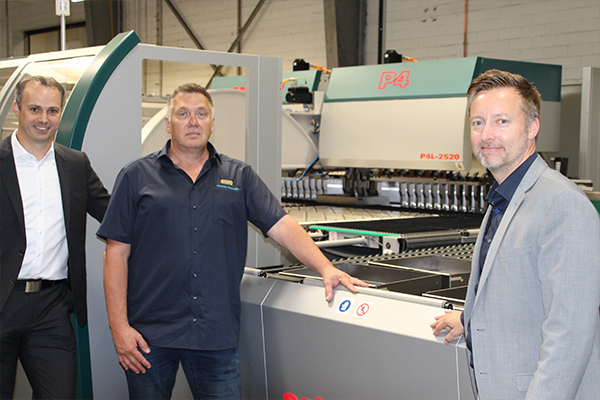
Case study
HAZET: high-quality output
With the growing need to meet high quality and a very high turnover rate standards, Hazet, a German company based in Remscheid, opted for 2 Salvagnini panel benders with high productivity and reliability, which allowed the company to reduce the target time by at least 20% and achieves repeatability accuracy of 1/10 mm with 1,000 drawers.
High-quality output
Highlights
- HAZET
Established in 1868 by Hermann Zerver, HAZET, a fifth generation family business, produces tools and workshop equipment of the highest quality currently with about 600 employees. With more than 6000 products manufactured in four plants, the company is a full-range supplier in this area. In sheet metal processing, the company punches and laser cuts between 45 and 60t of thin sheet metal per week. Currently, sheet metal production is used only for the Assistent® tool trolley division. - The context
The machinery for sheet metal processing includes a punch-laser combi machine and two punching systems. Everything has fully automated loading and unloading as well as individual sorting. Moreover, Hazet has invested in three manual press brakes and two panel benders. In particular, the panel benders must keep up with the necessary output. “If we produce 100 Assistent® tool trolleys in a day, for example, we need 700 drawers in various variants that must be bent” illustrates Christian Koschella, Plant Manager at HAZET. Marcel Klein, the Purchasing Manager, adds: “We have a very high turnover rate, therefore for our panel benders in addition to high throughput, reliability was also a very decisive criteria. Finally, we chose the market leader in panel benders, Salvagnini." - The project
The first panel bender, installed in 2021, is a P4-2120 with a maximum bending length of 2,180 mm, a maximum rotating diagonal of 2,500 mm, max. length of the incoming sheet of 2,495 mm and a maximum width of the incoming sheet of 1,524 mm. An even larger system, a P4-2520, was installed in 2023. It has a maximum bending length of 2,500 mm, maximum rotating diagonal of 3,200 mm, maximum length of the incoming sheet of 3,050 mm and a maximum width of the incoming sheet of 1,524 mm. The systems are also equipped with an automatic loading station, sheet metal thickness check, automatic sheet metal feeding and a brushing station. The P4-2120 also has suitable tools for different bending procedures and single parts sorting at the end.
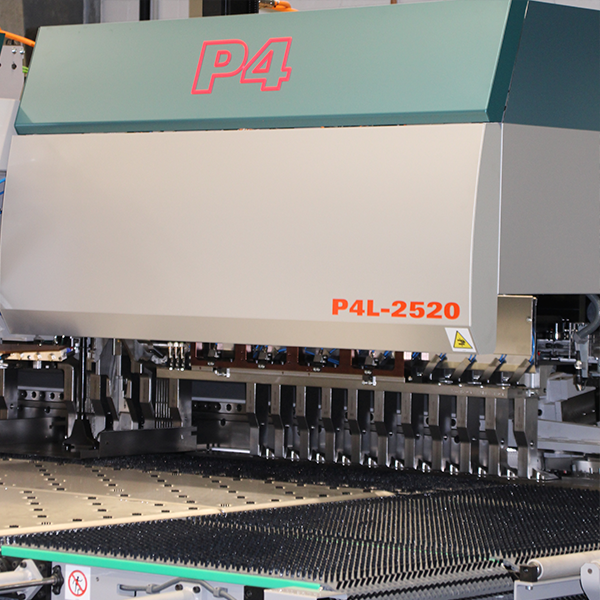