Simply the line
Automatically punches, cuts and bends sheet metal without intermediate handling. The ideal solution for any production strategy, be it kit, single-batch or series production.
100% flexible automation
The S4+P4 line punches, shears and bends sheet metal totally automatically, without any intermediate handling. Among other benefits, the line allows to produce on demand and just in time, to increase capacity and velocity, to reduce lead time, to process different materials without retooling, to optimize manpower activities.
Product overview
The integrated adaptive technologies make the S4 intelligent and able to automatically adapt to variations, eliminating waste and corrections, while guaranteeing high machining quality:
- the centering control system measures the incoming sheet and adapts the program to the actual dimensions measured, if necessary;
- the manipulator changes its dynamics according to the size and weight of the sheet, opening the pincers according to the percentage of sheet machined;
- an automatic system checks the thermal expansion of the manipulator’s axes and compensates any variations, guaranteeing extreme positioning precision;
- the shear automatically records the clearance and, depending on the thickness and the material, modulates the required force in-cycle.
Storage and automatic loading/unloading devices increase the autonomy of the system, regaining efficiency both in individual processing steps and throughout the production process. The wide range meets practically any layout or configuration requirements, adapting to the most diverse production strategies.
The S4 punching-shearing center maximizes process efficiency: all the loading, punching, forming, separation and unloading operations are automatic, done by a single system that eliminates semi-finished parts, does not require manual intervention and assures extreme repeatability.
The P4 uses universal bending tools which automatically adapt in-cycle to the panel geometry, without machine down times or manual retooling, allowing batch-one or kit productions.
The integrated adaptive technologies (advanced sensors, bending formula, MAC3.0) make the system intelligent and able to automatically adapt to changes in the material and the external environment, eliminating waste and corrections, and extending the range of products that can be made.
The P4 offers customized solutions, including auxiliary tools and additional devices for special geometries or different loading/ unloading solutions.
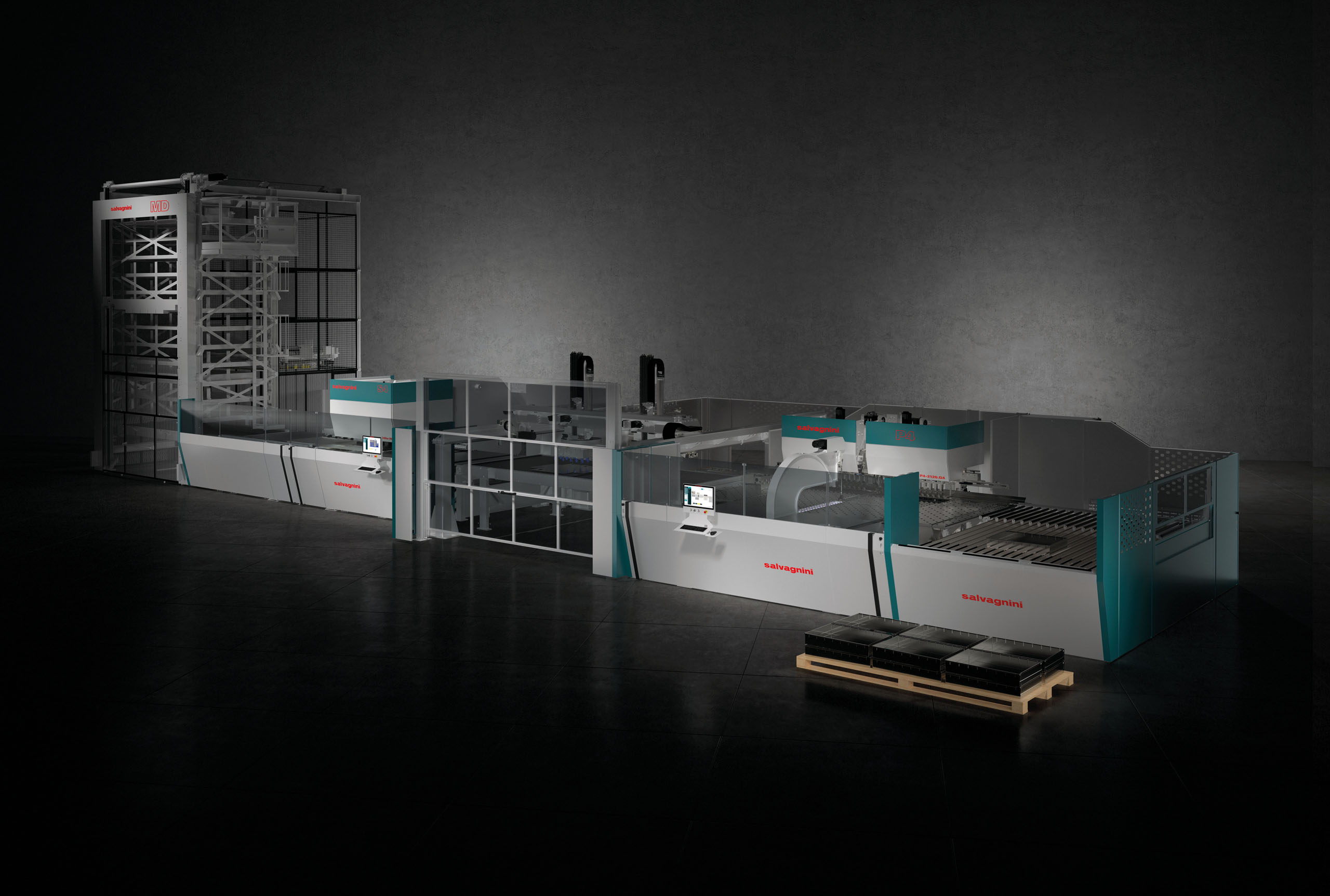
MAC3.0
MAC3.0 detects any differences in the mechanical characteristics of the material compared to their nominal value during the cycle, adapting the movements of the bending unit and the manipulator to compensate them.
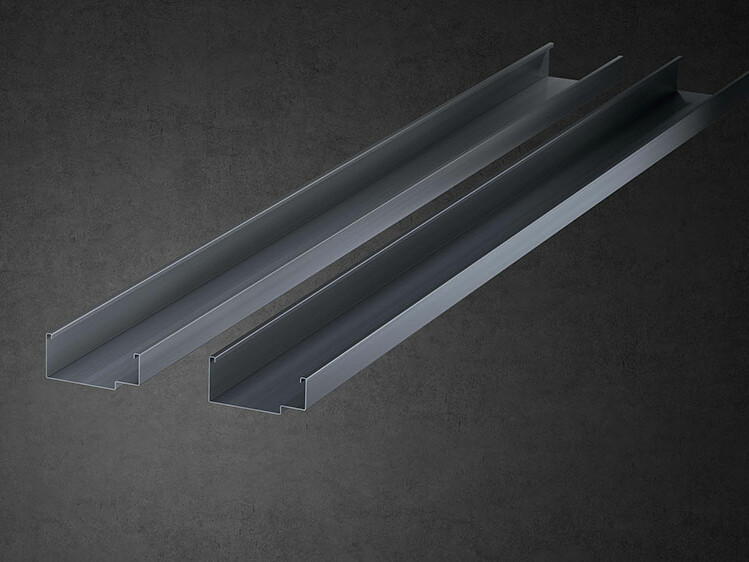
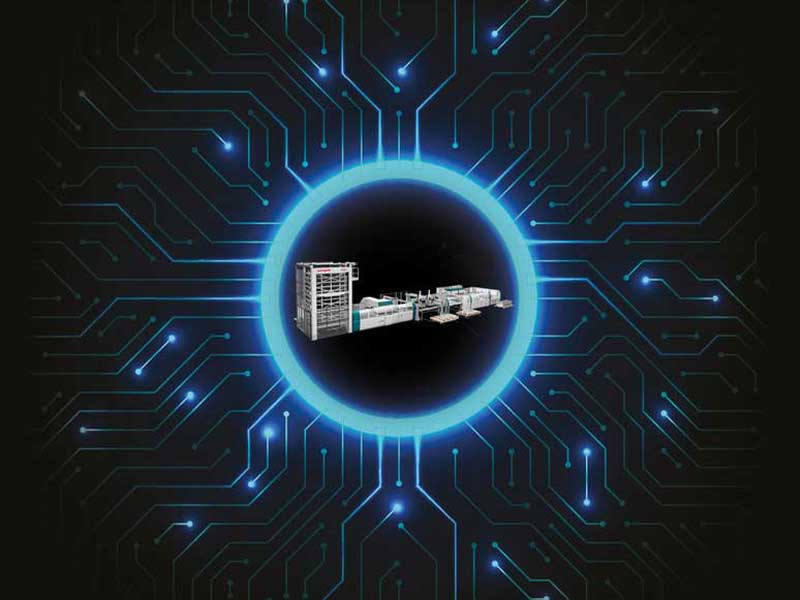
Industry 4.0
Digital transformation and Industry 4.0 are key topics for staying competitive on the market. When adopted, they can implement and manage complex, integrated, highly automated high-performance systems, and can help to develop simple solutions that require no structural changes to the production layout, making the world of smart manufacturing much more accessible.
Software
Industry has changed: flexibility and efficiency are fundamental requirements for managing increasingly smaller batches or rapid item turnover rate. And developments in technology have in some way upset the balance between workloads, with increasingly fast systems which however need to be guided by more and more specific machine programs, the generation of which is increasingly time-consuming. This is why software is increasingly crucial to improving the efficiency of machinery.
Salvagnini’s IoT solution, increases the global efficiency of the line. LINKS allows real-time monitoring of the machine’s performance and independent analysis.
Ready to dive in?